The bow is birch.
1. The pair of carved Ravens hold the cord in their beaks. The tarred black #18 nylon seine line was too slippery so it was replaced with boot lace. That spins the drills in both directions very well.
2. Both the hearth board and the drills are very dry western red cedar sapwood. I have lots of that, making more is easy.
3. I buy the blades for the Pacific Northwest style wood carving tools and make up all the wood work myself.
4. I'm sure everybody recognizes everything.
5. I am open to suggestions to see embers instead of nothing but a whole lot of smoke! For example, look carefully at the drill diameters. More?
1. The pair of carved Ravens hold the cord in their beaks. The tarred black #18 nylon seine line was too slippery so it was replaced with boot lace. That spins the drills in both directions very well.
2. Both the hearth board and the drills are very dry western red cedar sapwood. I have lots of that, making more is easy.
3. I buy the blades for the Pacific Northwest style wood carving tools and make up all the wood work myself.
4. I'm sure everybody recognizes everything.
5. I am open to suggestions to see embers instead of nothing but a whole lot of smoke! For example, look carefully at the drill diameters. More?
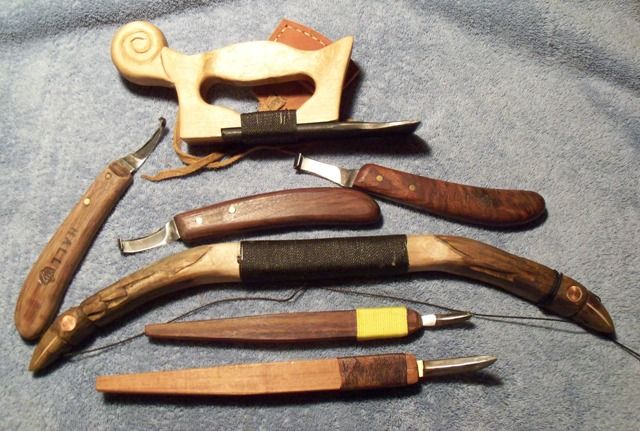
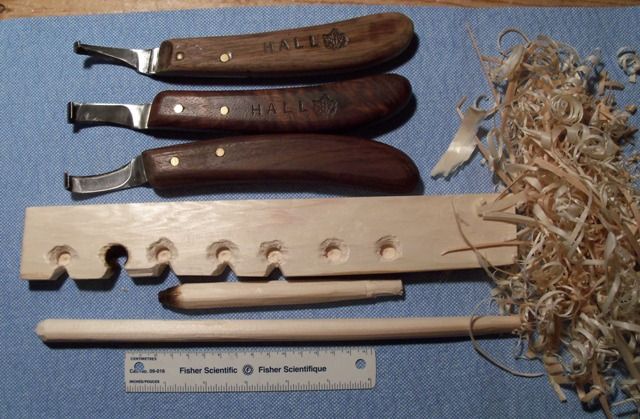
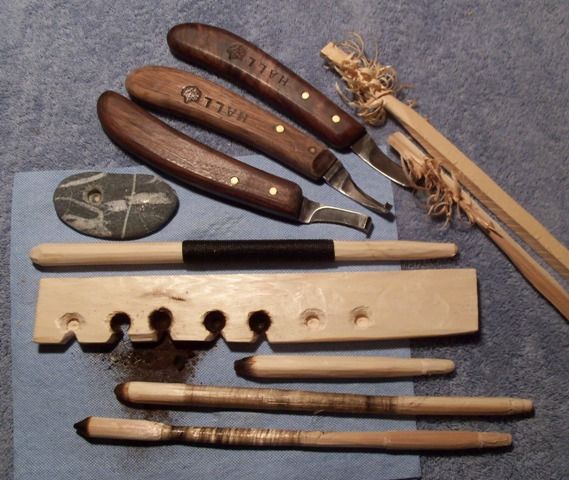
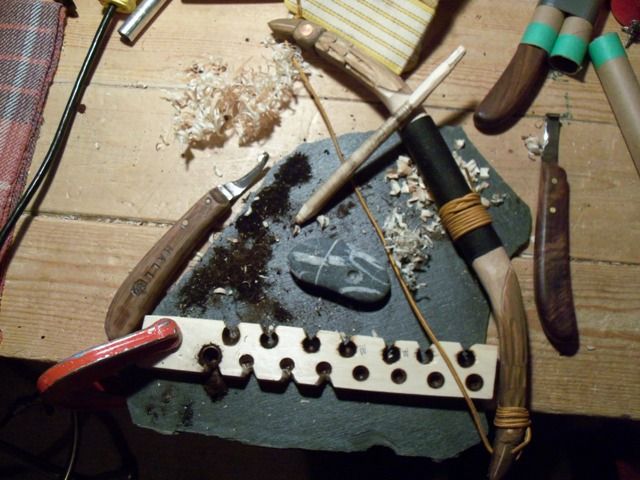
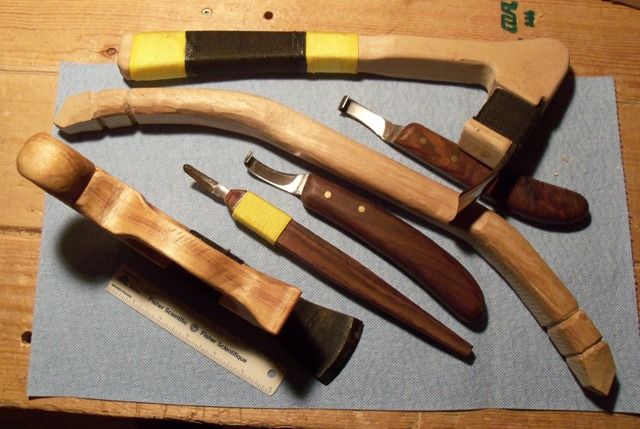