By a round about way I found I wanted to melt copper - to make tips for atlatl darts by repeatedly dipping them in molten copper of course. I thought about the opinion that wood fire doesn't get hot enough to melt copper (or get it from its ore). I decided to have a go.
Here it is:-
And here is the copper wire I succeeded in melting:-
and here is what happened to the bottom of a green glass bottom along the way:-
So I have proved it can be done. But I didn't get anything like a whole mass of copper melted. That would be for Mark II. Any suggestions on an improved design?
The furnace is 3 logs stood upright over a 3-4 inch hole in the bottom of an old barbecue and wedged and packed around with more wood.
I think the copper only melted when I put the piece of glass over the top and may have acted as a lid.
Here it is:-
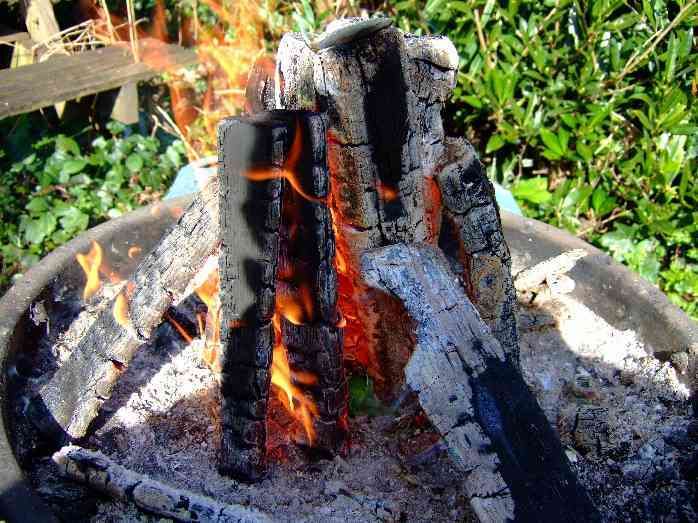
And here is the copper wire I succeeded in melting:-
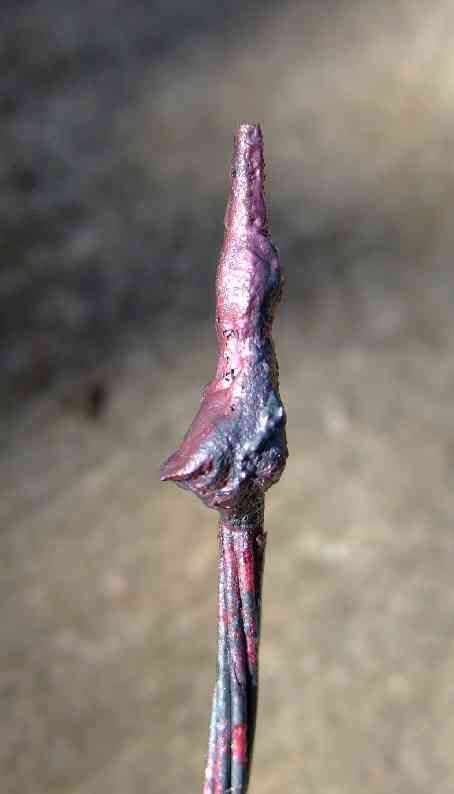
and here is what happened to the bottom of a green glass bottom along the way:-
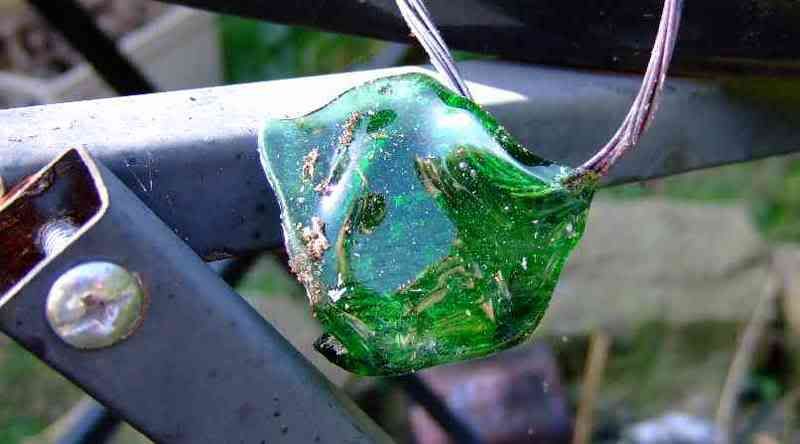
So I have proved it can be done. But I didn't get anything like a whole mass of copper melted. That would be for Mark II. Any suggestions on an improved design?
The furnace is 3 logs stood upright over a 3-4 inch hole in the bottom of an old barbecue and wedged and packed around with more wood.
I think the copper only melted when I put the piece of glass over the top and may have acted as a lid.