So, I've volunteered myself to make knifes. Well, teach others to. So need to work out how to do it myself.
I've done some tracing on some knife blanks and I think I like this one.
I'm cutting it out on our "Wazer" which is a hobbyist waterjet cutter. Much more bushcrafty than an angle grinder because we're just using water and sand to cut with. Well, gem stone. The cost of the cut is £7.50, but I can check this works before getting a bunch cut on a laser.
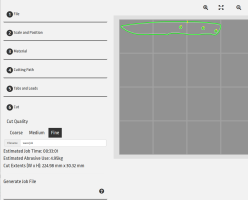
I've done some tracing on some knife blanks and I think I like this one.
I'm cutting it out on our "Wazer" which is a hobbyist waterjet cutter. Much more bushcrafty than an angle grinder because we're just using water and sand to cut with. Well, gem stone. The cost of the cut is £7.50, but I can check this works before getting a bunch cut on a laser.
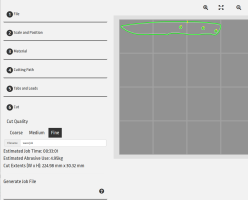