Following on from the thread about some Iron Age knives that I've made recently, there have been questions about the shear steel I used in the blades. Well, since I've been infront of the computer and I can only deal with so many emails in one sitting, I thought I would jot a few things down about the process 
First off. Shear steel is the name given to steel produced by adding carbon to iron through cementation, that is to say iron is soaked in a carbon rich evironment at temperatures that allow the migration of the carbon atoms. This method is as old as the Iron Age and was the principle way of obtaining steel until the industrial revolution. In its simplest form carborisation of a bit of steel can be done by keeping the iron hot (over 840C) in the right part of the forge for a good while. Easier said than done because while the temperature is easy to maintain, the amount of oxygen is not. The carbon will migrate both ways: reducing atmosphere and it goes into the iron; oxidising atmosphere and it moves out. Some Iron Age swords show that they were carborised in this way after forging (the outer skin shows higher carbon patches).
That process can be controlled to an extent by creating an airtight container around the iron and carbon. Files (and other small pieces) can be carborised (aka case hardening) by wrapping them in leather, followed by a clay shell, bringing up to temperature in the forge and left to soak for a while before plunging into water to harden. This only works for fairly small objects and a shallow layer of steel.
In order to make a lump of steel, a vessel needs to be made to contain pieces of iron. That container is then stuffed with a carbon rich material such as charcoal, leather, bone, etc and sealed up tight before placing in the forge and cooked. To give an idea of the time this takes to accomplish, carbon migrates at a rate of about 0.4mm per hour at the right temperature in a reducing atmosphere. So it is not a fast process! There are certain chemicals that speed up the absorption rate and they will also add other traces to the resulting steel. For example, horse dung (and other herbivorous poop) increases the rate nicely. This is the area of study that my MA thesis focussed on.
Here are some pics to break up the reading
The ingredients of this batch of steel: Wrought iron (old chain in this case), charcoal (birch from my woods) and poo (mostly roe deer, but may have some hare in there too)
The ingredients are put in a ceramic vessel (this was left over from uni and has now expired, so I now use welded up pipe like other smiths doo
), sealed with clay and cooked for sometime whilst forging stuff alongside. Ah the joy of gas!
Once I think its had long enough (bit of guessing), the pot is removed and opened.
If the iron has soaked up a goodly amount of carbon then the surface will be covered in bubbles and blisters. This is now known as Blister Steel, for obvious resons. The observant amongst you will spot that the last picture has different pieces of metal than the first. Thats because they are pictures from a different batch. oops. the smaller pieces are strap hinge and were in the ceramic vessel pictured, the larger (chain) pieces are wating to be forged into a blade or three.
Anyway. The blister steel has a high carbon skin and the rest is still low carbon iron, so not all that useful unless you are making something with an edge on one side like a chisel. Even then, the carbon distribution and structure of the metal is a bit hetrogenious to be very good. So further refinement is in order. This is done by folding the bar in half, or in this case, stackign the bars up and welding them together into a billet. The high temperatures of welding and the time at forging temperature allow the carbon to diffuse a bit, giving a more uniform material: Shear Steel.
The shear steel can be folded and rewelded to even out the carbon further, this is known as Double Shear Steel.
When folded once more it is, yep, Triple Shear Steel.
Wrought iron is a fibrous material like wood, the fibres being glassy slag stringers (that is what you see when you see a 'grain' in wrought iron). When you fold and reweld iron, the slag is molten and squeezed out of the metal. So the more times a piece of iron if folded, the cleaner and better its quality Railing is lower quality iron than chain, so is more slaggy to begin with as its not been as highly wrought: ie not had so much celaning in the factory. By the time you have the Triple Shear steel most of this slag has already been excluded, hence the much cleaner appearance despite the edge and back of the blade being made from the same parent material.
I've tweaked the etching with some ferric chloride on this blade before I repolished and etched more gently in vinegar. But it shows the layers well in this shot. You can also see where the carbon has migrated into the wrought iron back, this is where you have the dark (high C) line right above a thin pale line (low C). This happened because the carbon (like most things) will move from an area of high concentration to an area of low until the whole is uniform (rest of edge is shades of grey). So the time that the blade was at welding and final forging heats allowed this diffusion
If anybody wants to see what this stuff looks like under a microscope I can dig out some pictures from the experiments I did in the lab a decade ago
I plan to play with some of the shear steel I have already made up over the next few weeks. If there is interest I can add to this thread the construction of a blade from the shear steel and iron?

First off. Shear steel is the name given to steel produced by adding carbon to iron through cementation, that is to say iron is soaked in a carbon rich evironment at temperatures that allow the migration of the carbon atoms. This method is as old as the Iron Age and was the principle way of obtaining steel until the industrial revolution. In its simplest form carborisation of a bit of steel can be done by keeping the iron hot (over 840C) in the right part of the forge for a good while. Easier said than done because while the temperature is easy to maintain, the amount of oxygen is not. The carbon will migrate both ways: reducing atmosphere and it goes into the iron; oxidising atmosphere and it moves out. Some Iron Age swords show that they were carborised in this way after forging (the outer skin shows higher carbon patches).
That process can be controlled to an extent by creating an airtight container around the iron and carbon. Files (and other small pieces) can be carborised (aka case hardening) by wrapping them in leather, followed by a clay shell, bringing up to temperature in the forge and left to soak for a while before plunging into water to harden. This only works for fairly small objects and a shallow layer of steel.
In order to make a lump of steel, a vessel needs to be made to contain pieces of iron. That container is then stuffed with a carbon rich material such as charcoal, leather, bone, etc and sealed up tight before placing in the forge and cooked. To give an idea of the time this takes to accomplish, carbon migrates at a rate of about 0.4mm per hour at the right temperature in a reducing atmosphere. So it is not a fast process! There are certain chemicals that speed up the absorption rate and they will also add other traces to the resulting steel. For example, horse dung (and other herbivorous poop) increases the rate nicely. This is the area of study that my MA thesis focussed on.
Here are some pics to break up the reading

The ingredients of this batch of steel: Wrought iron (old chain in this case), charcoal (birch from my woods) and poo (mostly roe deer, but may have some hare in there too)
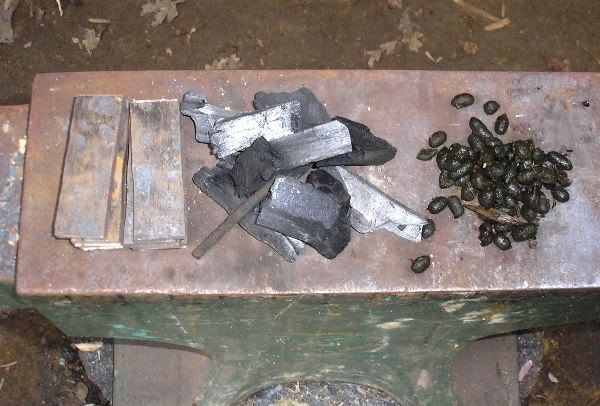
The ingredients are put in a ceramic vessel (this was left over from uni and has now expired, so I now use welded up pipe like other smiths doo

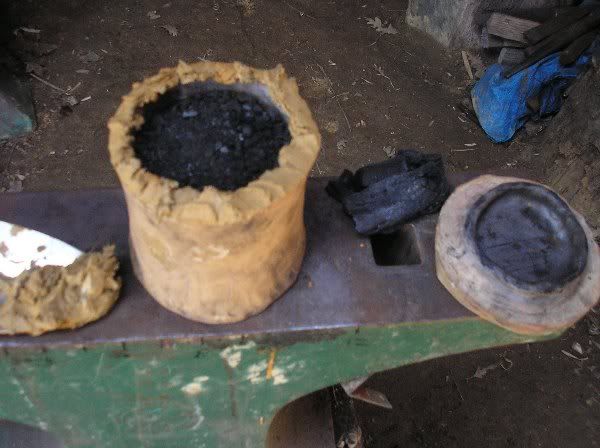
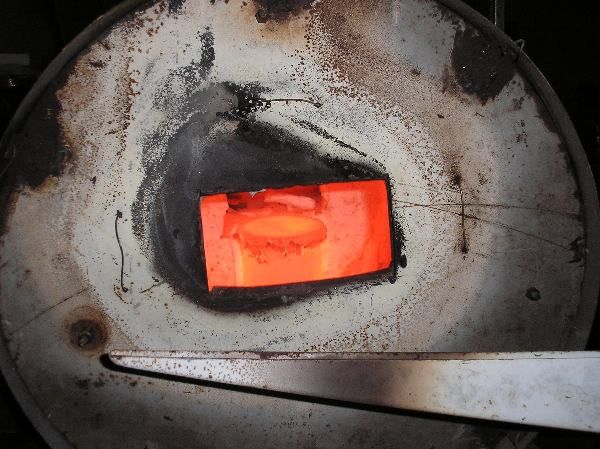
Once I think its had long enough (bit of guessing), the pot is removed and opened.
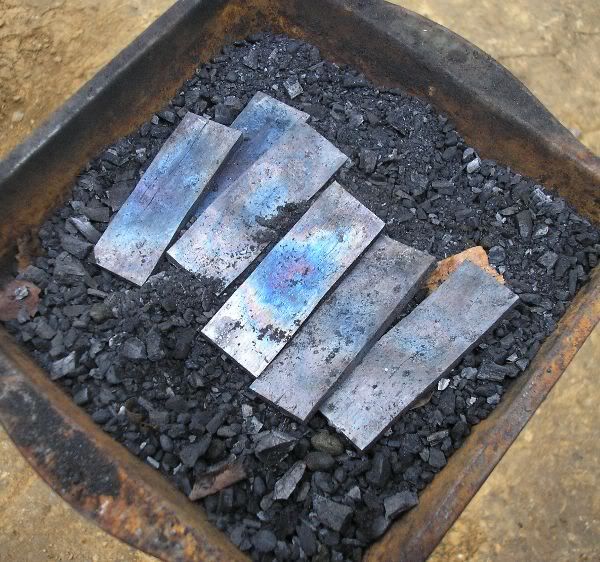
If the iron has soaked up a goodly amount of carbon then the surface will be covered in bubbles and blisters. This is now known as Blister Steel, for obvious resons. The observant amongst you will spot that the last picture has different pieces of metal than the first. Thats because they are pictures from a different batch. oops. the smaller pieces are strap hinge and were in the ceramic vessel pictured, the larger (chain) pieces are wating to be forged into a blade or three.
Anyway. The blister steel has a high carbon skin and the rest is still low carbon iron, so not all that useful unless you are making something with an edge on one side like a chisel. Even then, the carbon distribution and structure of the metal is a bit hetrogenious to be very good. So further refinement is in order. This is done by folding the bar in half, or in this case, stackign the bars up and welding them together into a billet. The high temperatures of welding and the time at forging temperature allow the carbon to diffuse a bit, giving a more uniform material: Shear Steel.
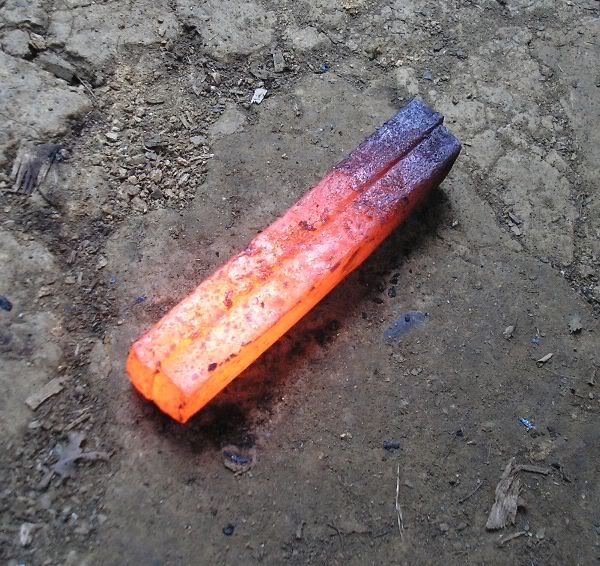
The shear steel can be folded and rewelded to even out the carbon further, this is known as Double Shear Steel.
When folded once more it is, yep, Triple Shear Steel.
Wrought iron is a fibrous material like wood, the fibres being glassy slag stringers (that is what you see when you see a 'grain' in wrought iron). When you fold and reweld iron, the slag is molten and squeezed out of the metal. So the more times a piece of iron if folded, the cleaner and better its quality Railing is lower quality iron than chain, so is more slaggy to begin with as its not been as highly wrought: ie not had so much celaning in the factory. By the time you have the Triple Shear steel most of this slag has already been excluded, hence the much cleaner appearance despite the edge and back of the blade being made from the same parent material.
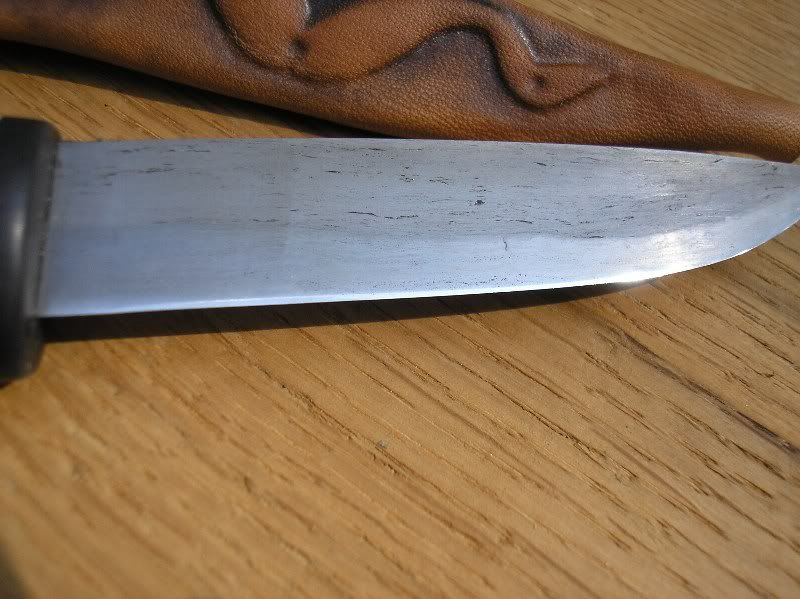
I've tweaked the etching with some ferric chloride on this blade before I repolished and etched more gently in vinegar. But it shows the layers well in this shot. You can also see where the carbon has migrated into the wrought iron back, this is where you have the dark (high C) line right above a thin pale line (low C). This happened because the carbon (like most things) will move from an area of high concentration to an area of low until the whole is uniform (rest of edge is shades of grey). So the time that the blade was at welding and final forging heats allowed this diffusion

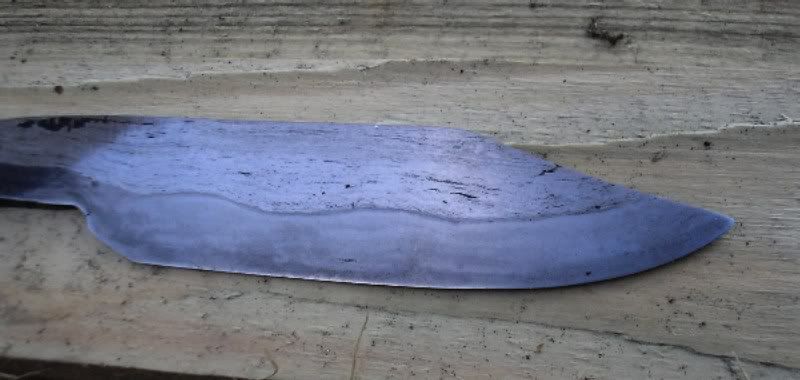
If anybody wants to see what this stuff looks like under a microscope I can dig out some pictures from the experiments I did in the lab a decade ago

I plan to play with some of the shear steel I have already made up over the next few weeks. If there is interest I can add to this thread the construction of a blade from the shear steel and iron?