Well it took me a long time....a long time....too long....but I managed to make a pair of them....one nice one for My best Man and the 'Learning curve' kinfe, well for me
(well I put too many hours into it even if it was just to experiment on before making the 'gift knife' for my mate.
the gift....
the (unfinished) pair...
one handed opening grip...
Light cuts grip....
Heavier cuts grip....
Showing off the mammoth tooth spine grip...
Most important bottle opening grip....
The Kit of parts....
Cutting the tooth....
I forgot to say the blades came from.....can any one guess???
The spalted ash I harvested from a local woods....
Well If you read this much....THANKYOU!!!
ask away if you want any info.
Glad to be back in the Bushy fold.....
Mojo

the gift....
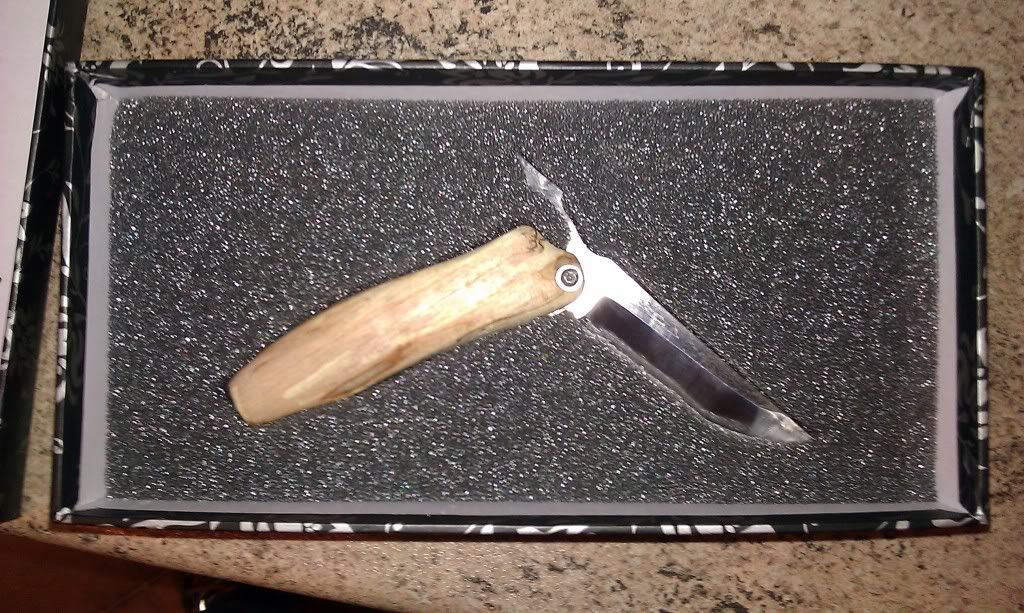
the (unfinished) pair...

one handed opening grip...
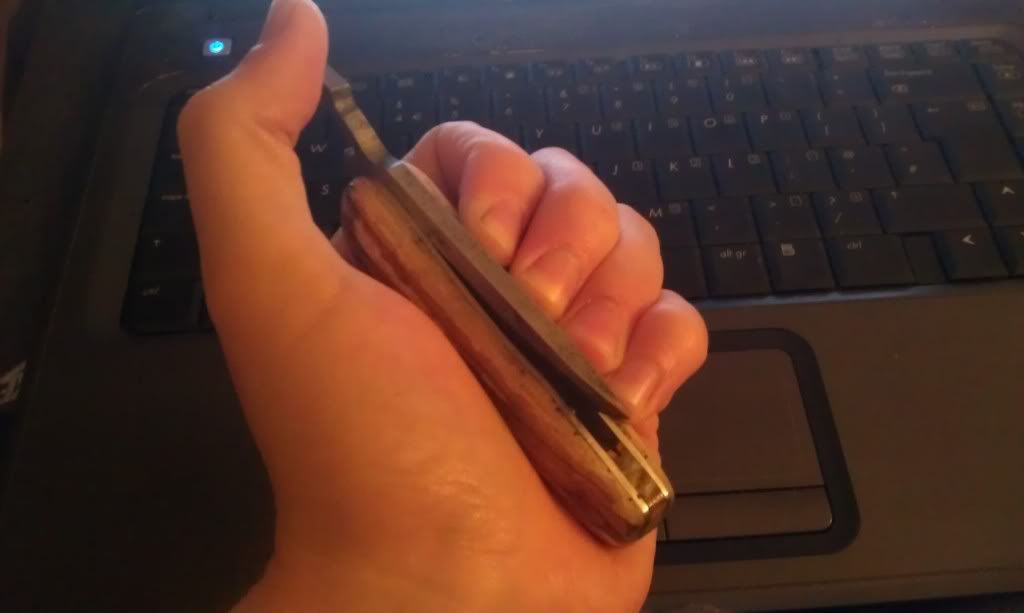
Light cuts grip....
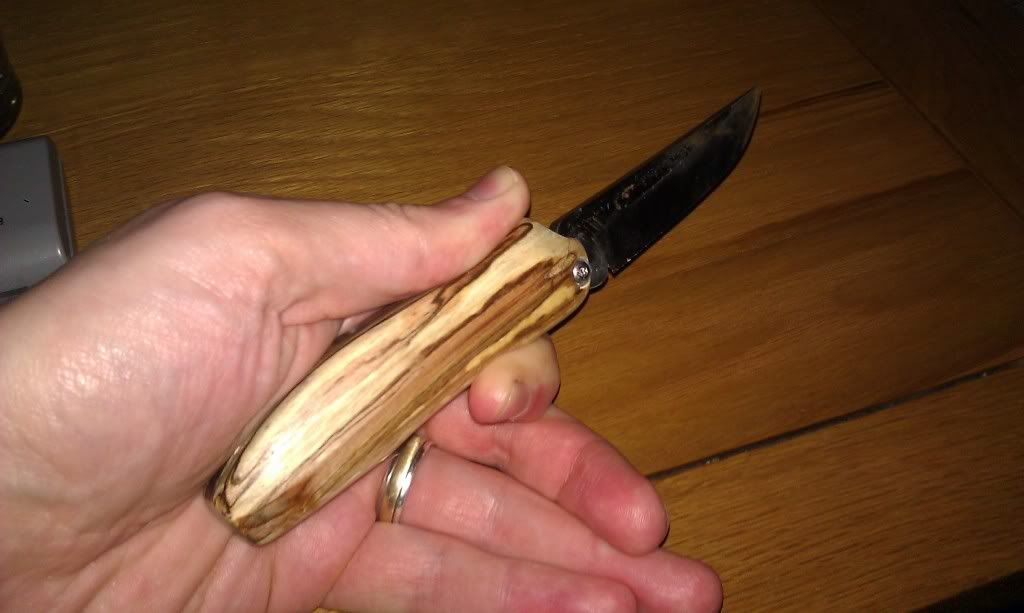
Heavier cuts grip....
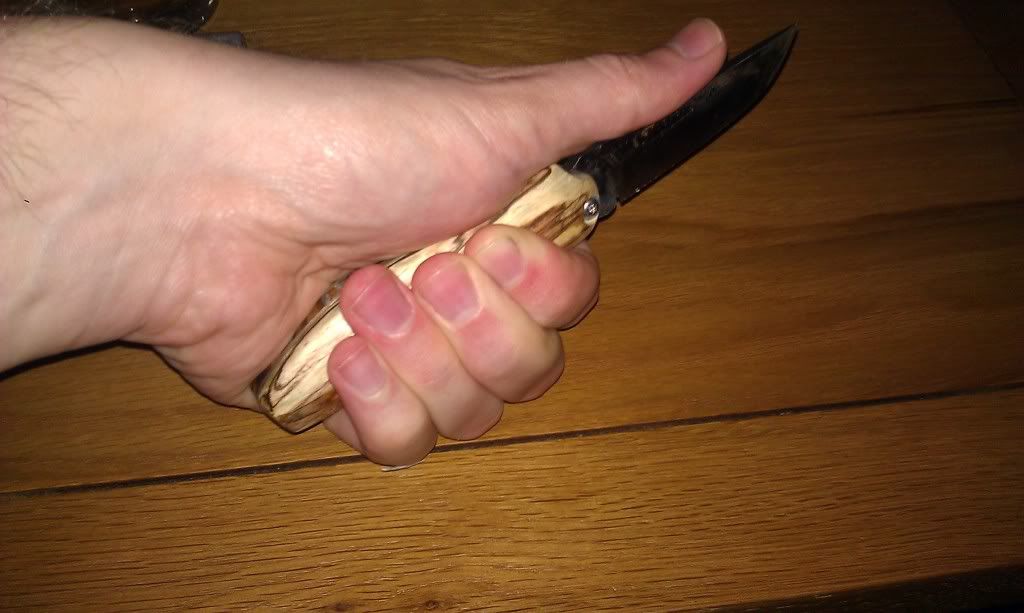
Showing off the mammoth tooth spine grip...
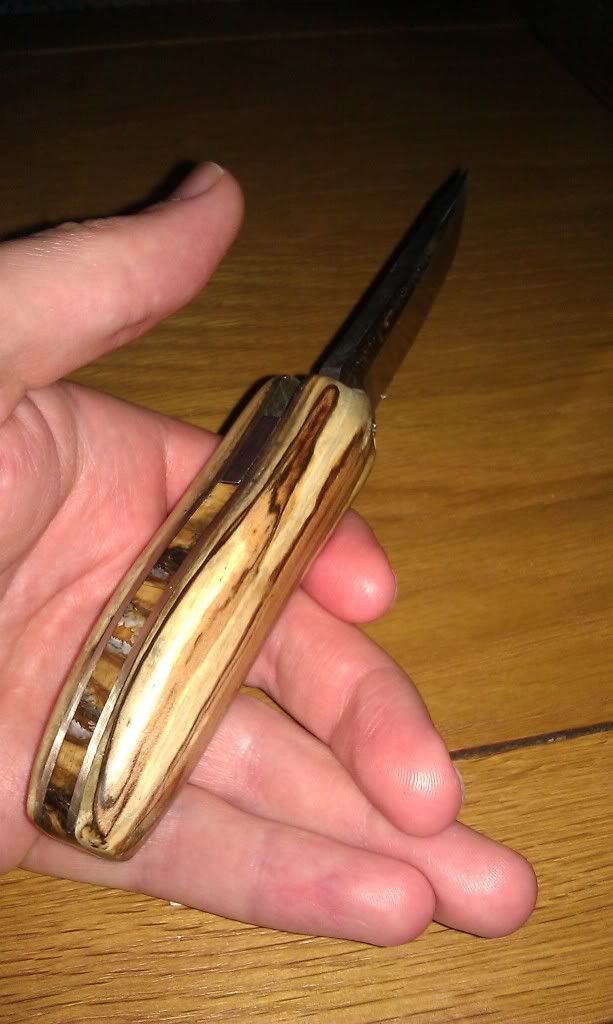
Most important bottle opening grip....
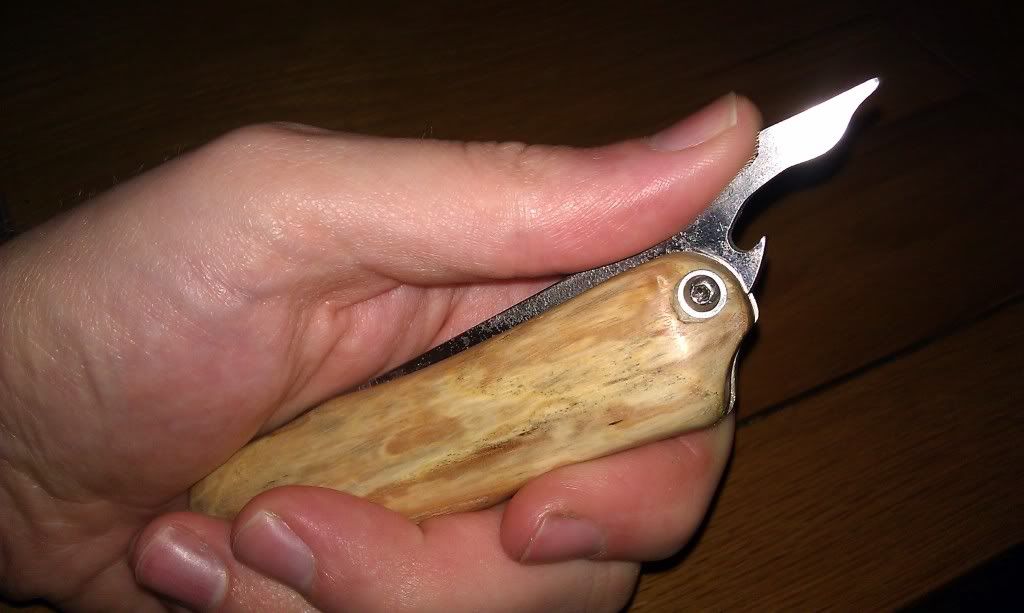
The Kit of parts....
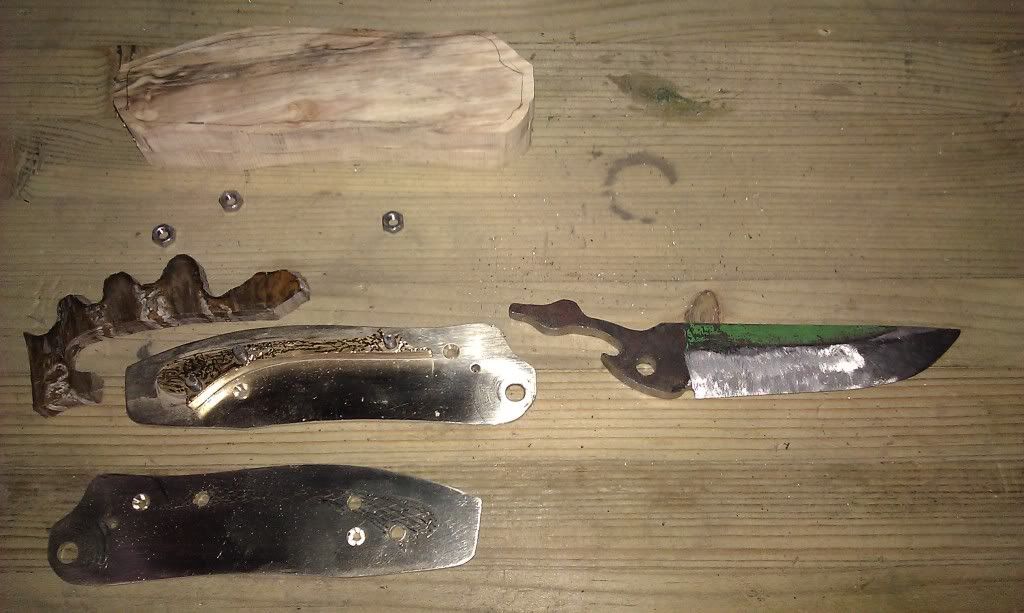
Cutting the tooth....
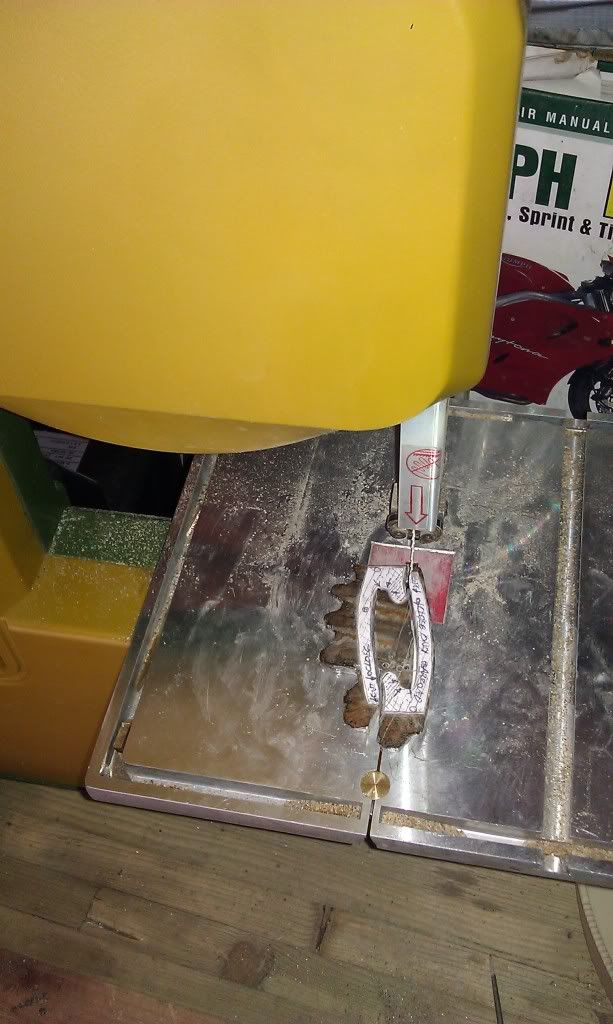
I forgot to say the blades came from.....can any one guess???
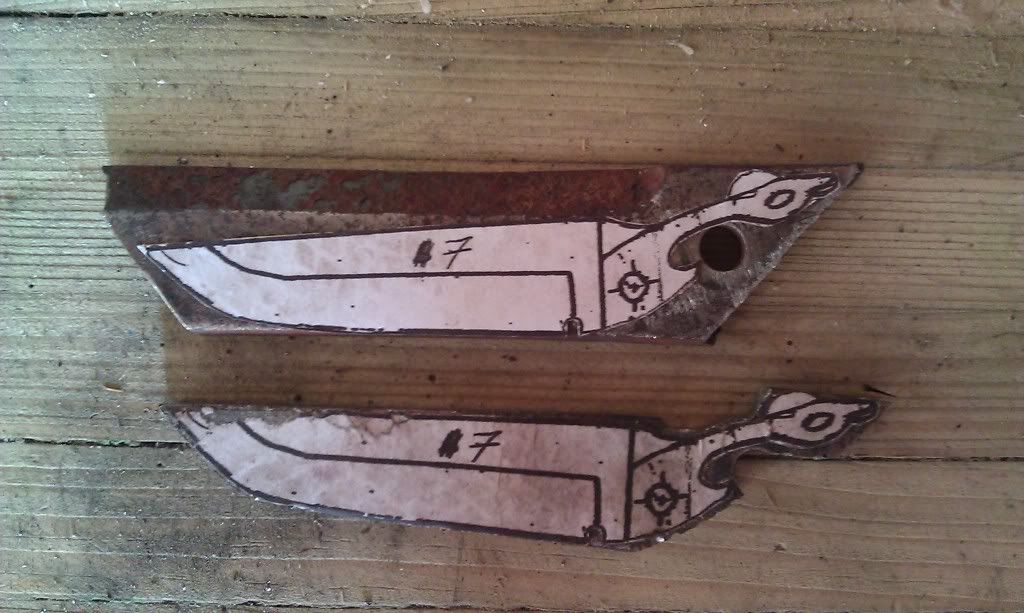
The spalted ash I harvested from a local woods....
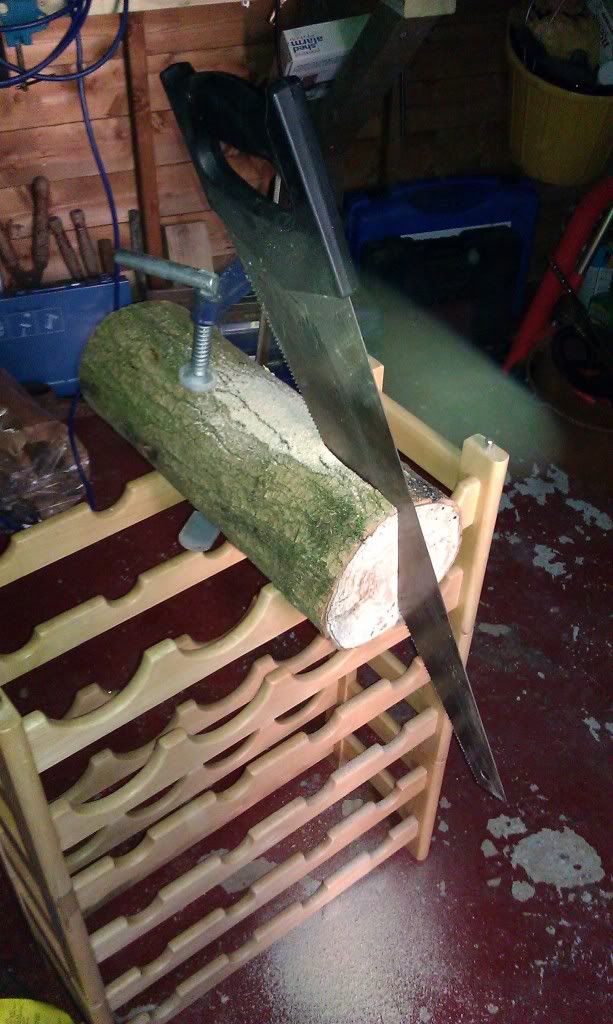
Well If you read this much....THANKYOU!!!
ask away if you want any info.
Glad to be back in the Bushy fold.....
Mojo
Last edited: