HI Everyone,
I am trying to make a copy of the Famous Hobo Stove By the Master Himself Mr Wayland. After searching for 4weeks i Finally found a size 12 stainless steel Container that will fit the 1o" inch Zebra Billy. I used a small nail punch 1/38 to marked the holes, so as not to dent the steel too much,then i went into my shed to get my 90drill bits set. But i am not able to drill the SHINY/SMOOTH/ SLIPPERY/ TOUGH/ STAINLESS STEEL , B....... THING CONTAINER. So i am back to square one again. Excuse my ignorance/ lack of Experience with STEEL! So what am i doing WRONG!
I am using HSS METAL DRILL BITS COATED WITH A BRASSY LOOKING PAINT.
Do I need to buy any special MAKE, TYPE, DRILL BITS apart from the ones i have!
Any Constructive ideas would be appreciated.
Taken a couple of pictures of the Billy and Stove.
Regards
the interceptor boy.
I am trying to make a copy of the Famous Hobo Stove By the Master Himself Mr Wayland. After searching for 4weeks i Finally found a size 12 stainless steel Container that will fit the 1o" inch Zebra Billy. I used a small nail punch 1/38 to marked the holes, so as not to dent the steel too much,then i went into my shed to get my 90drill bits set. But i am not able to drill the SHINY/SMOOTH/ SLIPPERY/ TOUGH/ STAINLESS STEEL , B....... THING CONTAINER. So i am back to square one again. Excuse my ignorance/ lack of Experience with STEEL! So what am i doing WRONG!
I am using HSS METAL DRILL BITS COATED WITH A BRASSY LOOKING PAINT.
Do I need to buy any special MAKE, TYPE, DRILL BITS apart from the ones i have!
Any Constructive ideas would be appreciated.
Taken a couple of pictures of the Billy and Stove.
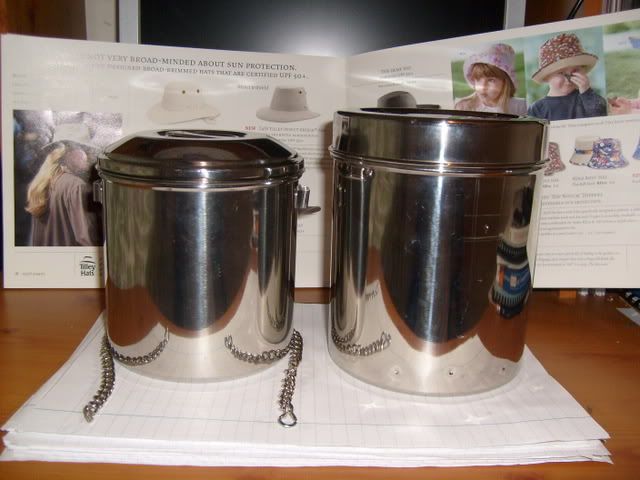

Regards
the interceptor boy.