Hi All,
Over the past month I have spent several afternoons with Sandy from Jacklore Knives as he shows me the process of building one of his Jacklore Classics bushcraft knives. It has been a pleasure to spend time with Sandy at his workshop and film the build of my knife.
[video=youtube_share;7t-MQqCZ8bM]https://youtu.be/7t-MQqCZ8bM[/video]
This is the knife that Sandy has built and gifted to me.
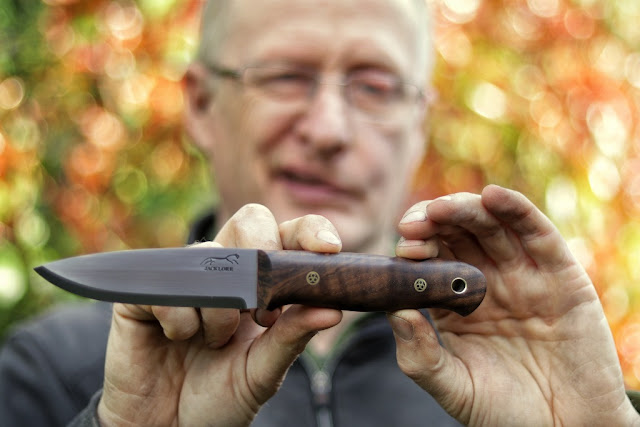
The knife was customised by enlarging the handle length and slightly reducing the blade length.
The German O1 tool steel was first roughly cut out on a metal workers band saw before the finer shaping work was done on the knife makers grinders. Sandy uses several different wheels for the contours of the handle. Watching Sandy using the grinders I could not believe how quickly they can remove material when O1 tool steal was in is softer pearlite state.
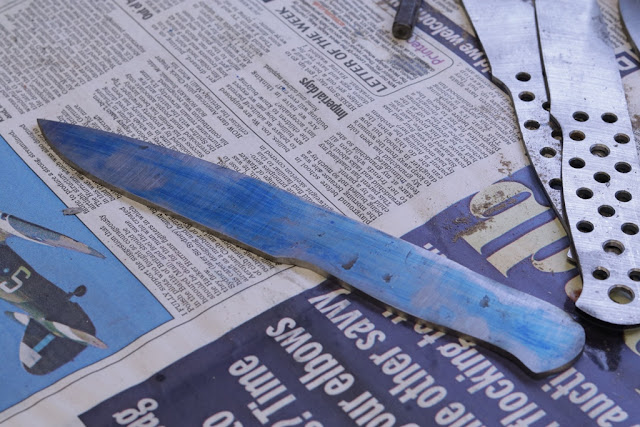
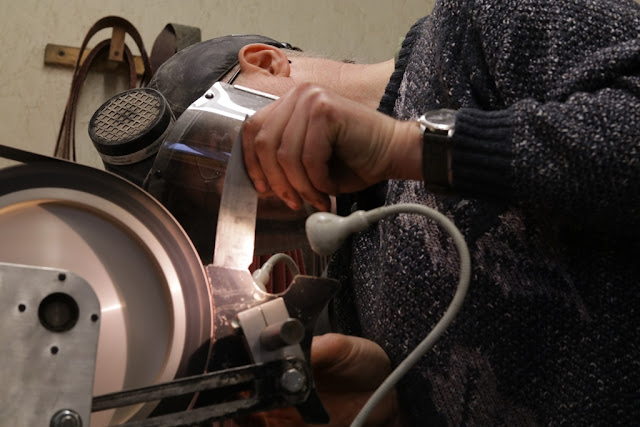
Once the handles had been drilled (for the pins and assist bonding for the scales) the blade was coated with an anti scale compound to stop loss of carbon to oxygen when the knife was in the kiln for the hardening process.
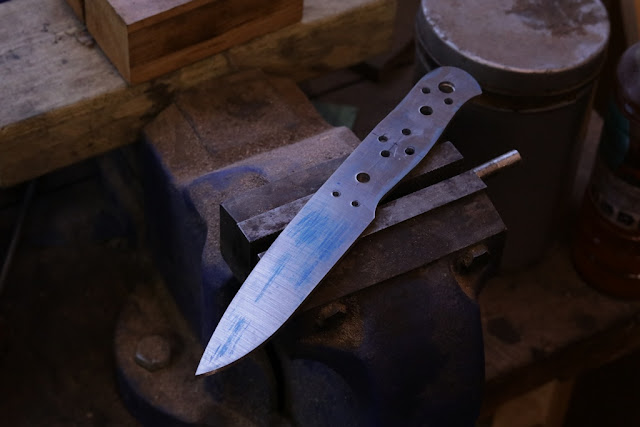
The knife blade was placed in a knife makers kiln for heat treating and quenching. The blade was check for any warps but all was straight and true.
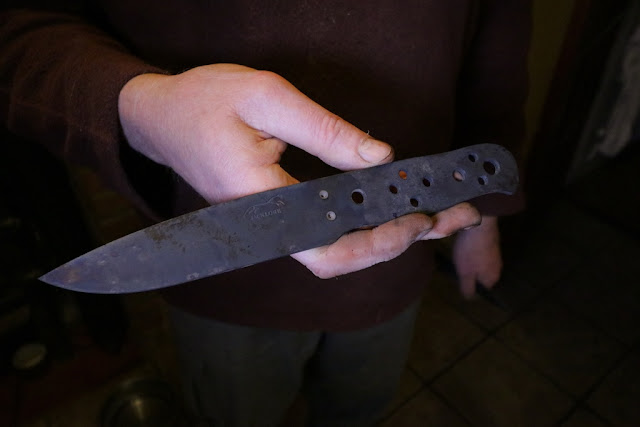
Liking a dark wood for a knife handle I choose some walnut for the scales of the knife which had previously been stabilised by Sandy. These were prepared and keyed up for bonding with the blade.
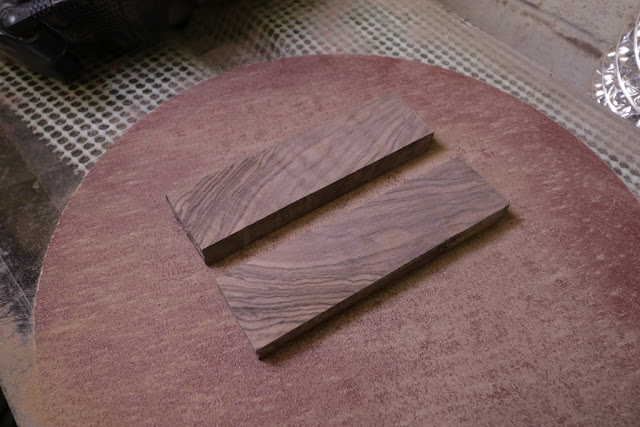
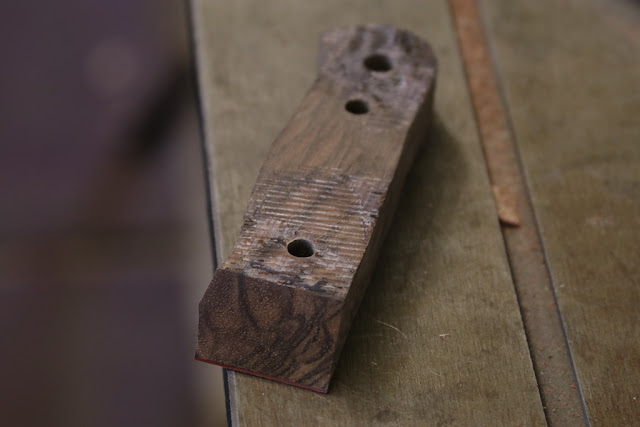
Before I left for the day the knife was placed in warming oven for its first temper cycle, returning a week later Sandy had completed the second and third tempering cycles.
The blade was then tested on a Rockwell hardness tester and measured 58/58.5Hrc along it length.
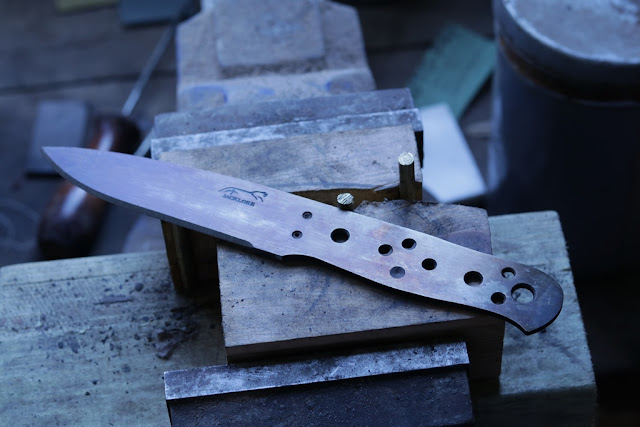
Back to the grinders to place the bevel on the blade, this was done at 28 degrees rather than Sandys favoured bevel angle of approx. 25 to 26 degrees.
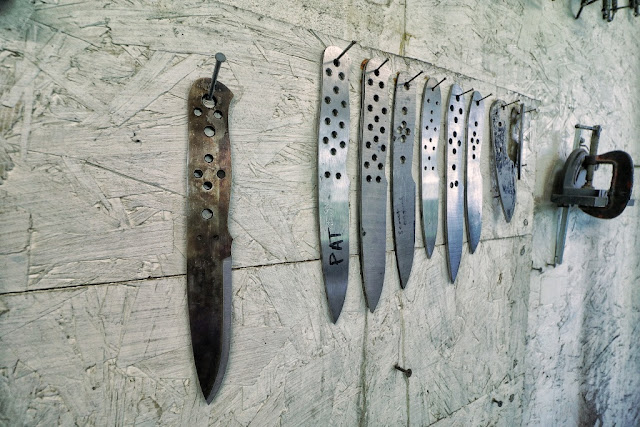
The scales were keyed up ready to attached to the blade and clamped in place to cure 24 hours.
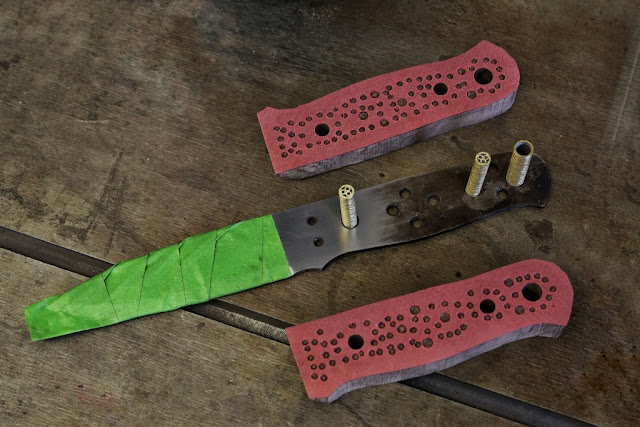
But it was another week before I could return to the workshop for the final stages of the build as Sandy shaped the handle adjusting to best suit my hand.
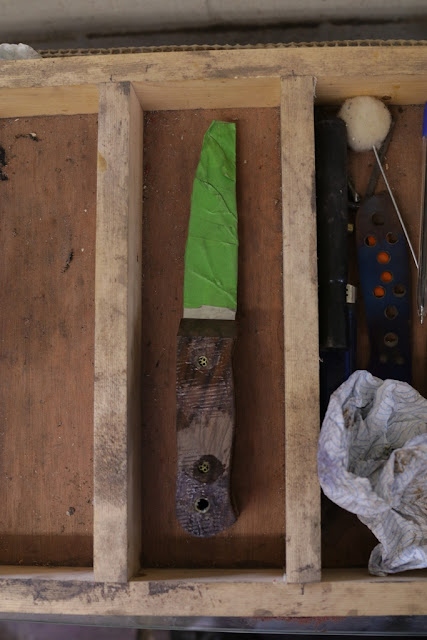
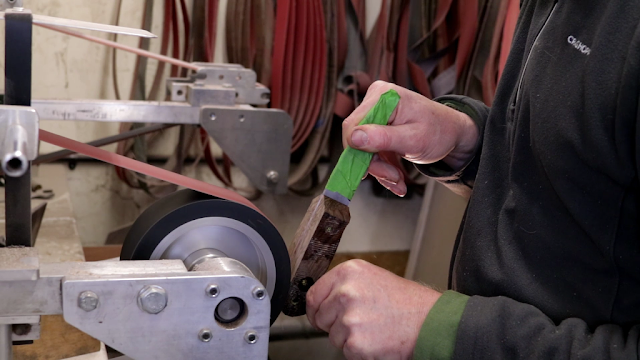
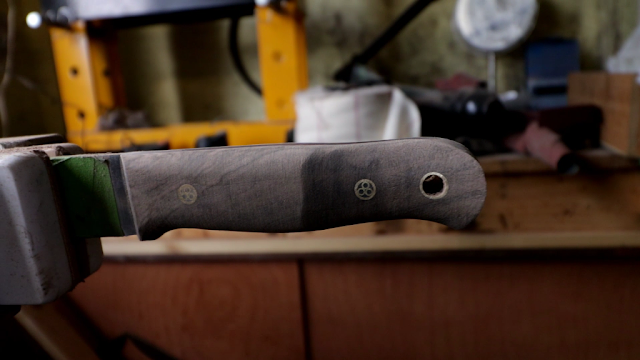
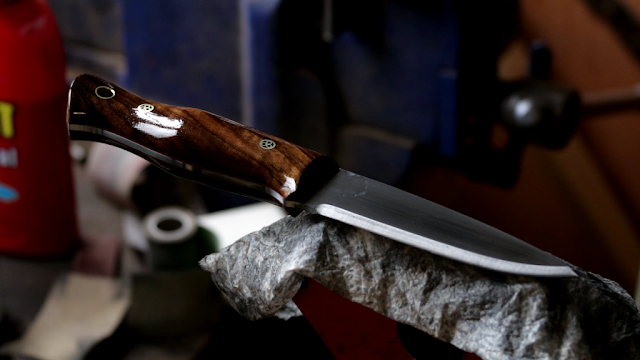
I was an absolute pleasure to spend the time with Sandy and a good friendship has grown though the building of this knife.
The finished Jacklore Classic
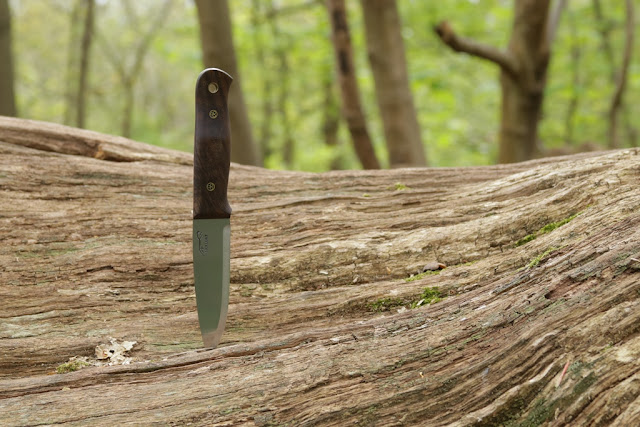
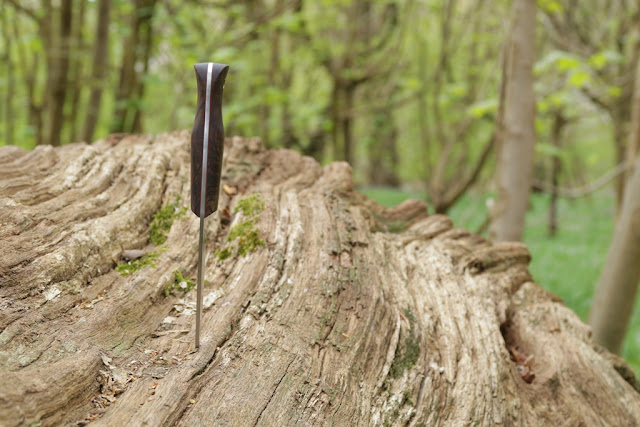
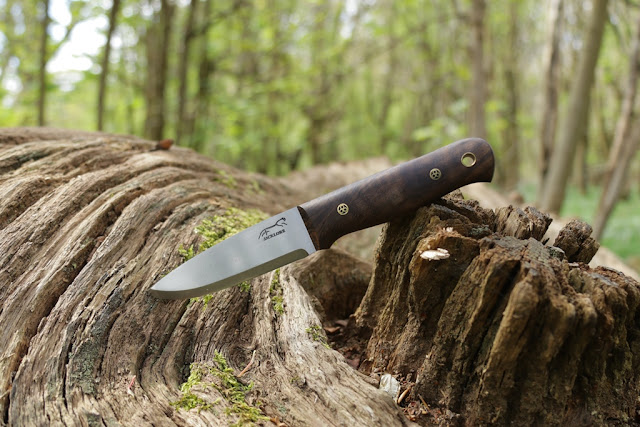
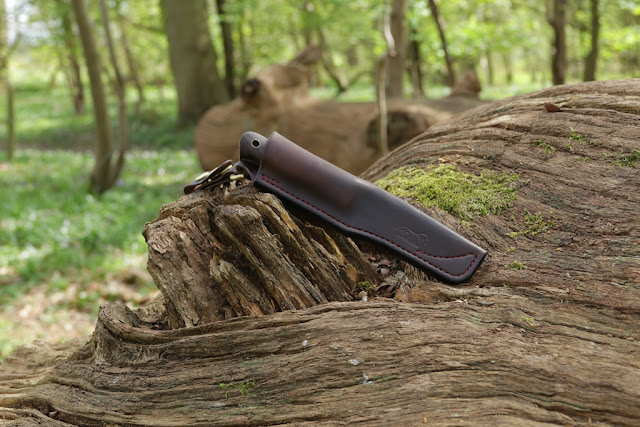
KNIFE SPECS
Metal - 3mm O1 Tool Steel (Heat treat 58/58.5 HRC)
Grind - Scani grind (28 deygree)
Scales - Stablised Walnut
Liners - Red
Pins - Jacklore Trinity Mosaic Pins
Brass lanyard tube
Browns Leather Sheath with brass D ring and dangler.
Over the past month I have spent several afternoons with Sandy from Jacklore Knives as he shows me the process of building one of his Jacklore Classics bushcraft knives. It has been a pleasure to spend time with Sandy at his workshop and film the build of my knife.
[video=youtube_share;7t-MQqCZ8bM]https://youtu.be/7t-MQqCZ8bM[/video]
This is the knife that Sandy has built and gifted to me.
The knife was customised by enlarging the handle length and slightly reducing the blade length.
The German O1 tool steel was first roughly cut out on a metal workers band saw before the finer shaping work was done on the knife makers grinders. Sandy uses several different wheels for the contours of the handle. Watching Sandy using the grinders I could not believe how quickly they can remove material when O1 tool steal was in is softer pearlite state.
Once the handles had been drilled (for the pins and assist bonding for the scales) the blade was coated with an anti scale compound to stop loss of carbon to oxygen when the knife was in the kiln for the hardening process.
The knife blade was placed in a knife makers kiln for heat treating and quenching. The blade was check for any warps but all was straight and true.
Liking a dark wood for a knife handle I choose some walnut for the scales of the knife which had previously been stabilised by Sandy. These were prepared and keyed up for bonding with the blade.
Before I left for the day the knife was placed in warming oven for its first temper cycle, returning a week later Sandy had completed the second and third tempering cycles.
The blade was then tested on a Rockwell hardness tester and measured 58/58.5Hrc along it length.
Back to the grinders to place the bevel on the blade, this was done at 28 degrees rather than Sandys favoured bevel angle of approx. 25 to 26 degrees.
The scales were keyed up ready to attached to the blade and clamped in place to cure 24 hours.
But it was another week before I could return to the workshop for the final stages of the build as Sandy shaped the handle adjusting to best suit my hand.
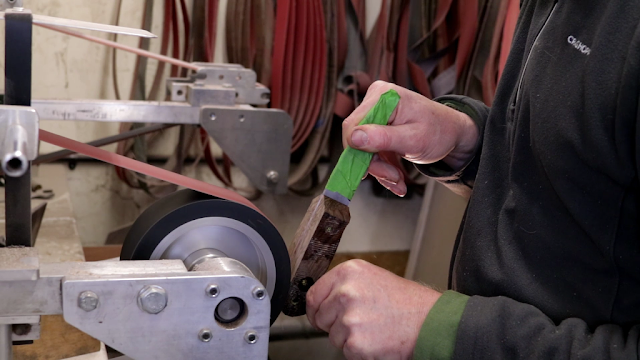
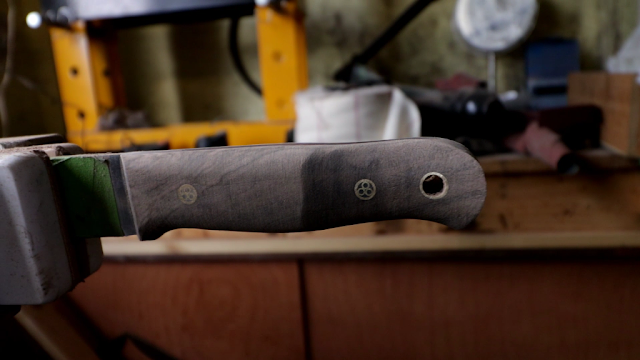
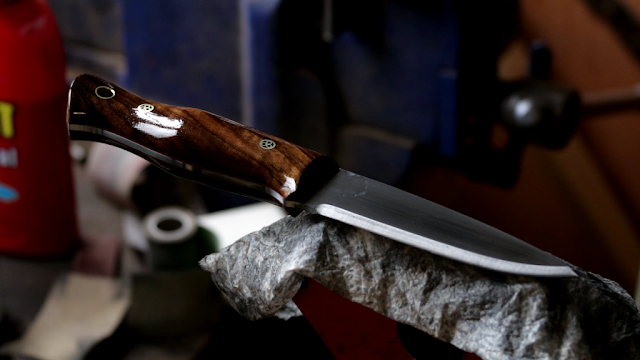
I was an absolute pleasure to spend the time with Sandy and a good friendship has grown though the building of this knife.
The finished Jacklore Classic
KNIFE SPECS
Metal - 3mm O1 Tool Steel (Heat treat 58/58.5 HRC)
Grind - Scani grind (28 deygree)
Scales - Stablised Walnut
Liners - Red
Pins - Jacklore Trinity Mosaic Pins
Brass lanyard tube
Browns Leather Sheath with brass D ring and dangler.