Cold formed hook tools
No bushcrafters’ tool kit would be complete without a spoon carving hook or three.
Normally these would be formed hot, when the steel is very soft, or at the very least cold bent with the steel in the annealed condition (ie also soft).
I’ll get on to hot work later, but I wanted to see whether I could make functioning hook knives from an old saw without needing a forge or blowtorch. I tested the idea on an offcut from the cheap hardpoint saw used before and it was easy enough to bend into a spoon hook, but this better quality Swedish saw took a bit more persuading (due to it’s higher hardness).
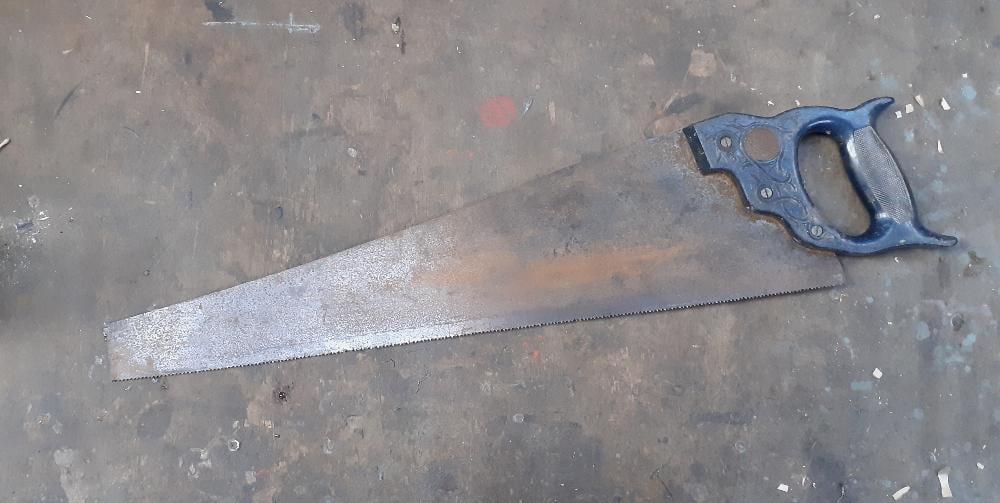
Cut from the saw
Starting with a strip approximately 15mm wide, I used a slightly open vice and a small hammer to shape it into a simple hook.
It is much easier to bend stiff metal into a depression than it is over a corner or bick (the pointy bit of an anvil). The key is to move the metal gently and don’t try to bend it too far in one stroke. A ballpeen works, but a cross peen hammer gives better control of the direction that the bend is going; just be sure to strike the metal at 90 degrees to the direction of the intended bend, otherwise the metal will twist.
Once the curve of the hook is completed, the crank to the handle can be made (either with the hammer or by placing the straight section in the vice and bending by hand). Some people file/grind the bevels before bending their hook blades, but I find they are more likely to twist or kink if you do; so I grind all of mine once the blade is bent to shape.
Once shaped, the edges of the blade can be ground (belt grinder if you have one) or filed flat and true. In this case I needed to remove a couple of mm to even everything up, which is why I started at 15mm 😉 Now the blade is shaped I grind/file the cutting edge on, though it may be easier to wait until the handle is in place.
Final sharpening is certainly best and safest done with a handle to hold onto (which is why the spoon hooks that I sell are ground but not honed unless they have a handle).
That was easy, but the thinness of the blade means that the hook is quite flexible. One way to resolve that is to bend the strip right over and form a loop knife, sometimes referred to as a scorp.
This time I bent the cranks first and then the curved section, starting in the centre and working out towards each end. As the curve progressed, the hammer fouled on the tangs, at which point they are brought together and clamped in a vice to complete the shaping. Since the steel is spring tempered, the loop keeps opening up, so I bound it closed with a little wire (which will be buried in the epoxy-filled hole of the handle). Bevels and a stick handle see the loop knife completed.
Tragsknarve
Here’s a tool that is little used these days. Known to me as a ‘tragsknarve’, it is basically a large scorp and is used for hollowing out bowls and the like when more control than an adze is required.
The shaping of the blade is exactly as with the loop knife, but since the handle soon fouls on the tangs I had to use a straight peen hammer. The hammer is an old boiler/chipping hammer but a very very dull axe could be used instead, or indeed a ballpeen if you are mindful of potential twists. The quick and dirty handle was a piece of 2×1” roofing batten that was sitting aound. Two nails run through the wood and two tangs, holding everything together. I wasn’t convinced by the strength of the wood, so bound it in string for good measure.
Traditionally the handles are often made from naturally grown Y-forks of wood, but at the time of making this, it was raining quite hard outside and I don’t like getting wet!
The blade is sharpened on one side in the same fashion as the loop knife and spoon hook.
Now for some gouges
At this point I wanted to make some gouges. I thought that since the saw blade was malleable enough to bend into the hooks and loops, then at least fairly shallow gouges would be possible cold.
Apparently not.
The next step will be hot forming!
Dave Budd is a world renowned smith specialising in historic weapons and other period steelwork, he runs knife and axe making courses amongst other things from his woodland in rural Devon.
You can see some of his work and contact him through his website DaveBudd.com
Leave A Comment
You must be logged in to post a comment.