Just back from demonstrating iron age leatherworking at the 'celts are coming' living history fair at the Scottish Crannog Centre on Loch Tay. It was a superb wee event, I had David Mcgovern of Monikie rock arts and Jon Mac woodcarver either side of me, and we had Neil Burridge casting bronze swords, some fellas doing bog iron refining, tablet weaving, Theresa Kamper with her skins and tanning gear, and Peter Annanin of Woodland Knowledge with more skins and tanning, and some iron age cooking/foods.
Beezer of this parish came up with me to help out as my assistant on my stall, and then we both stayed on for an extra two days to attend Neils bronze sword workshop where we all cast a sword together, then were each given a pre master cast blank to work on as our own.
The Crannog
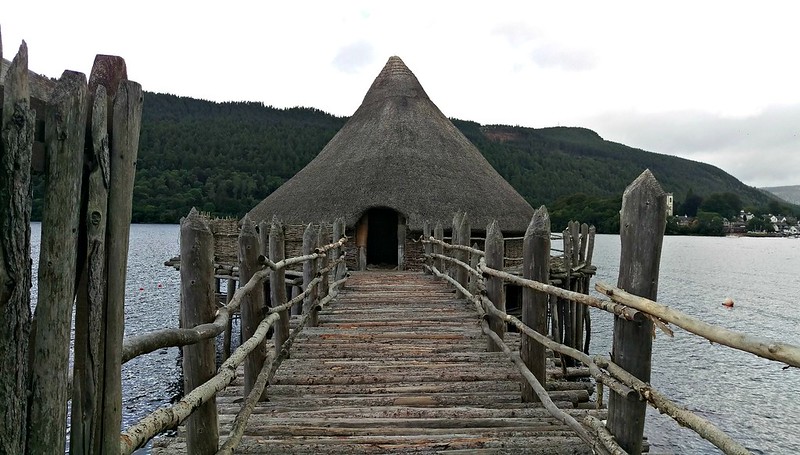
Stall
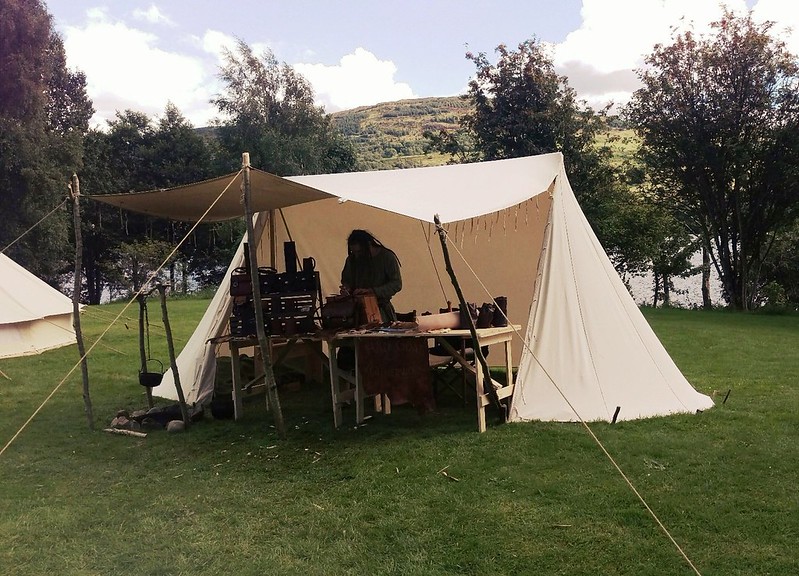
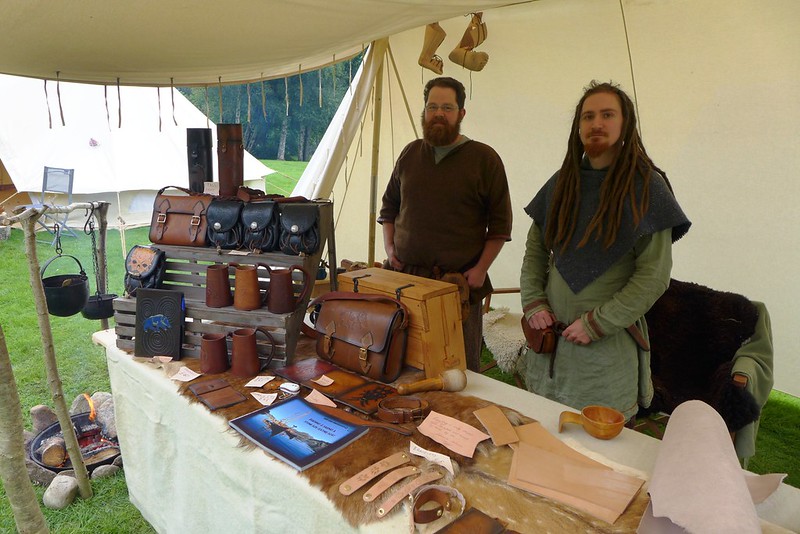
Log Boat
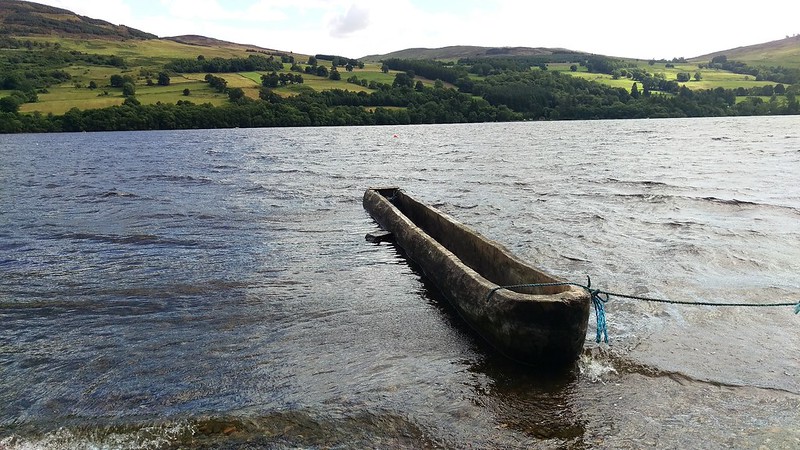

On to the bronze sword workshop. Only got a few pictures quickly snapped by me or Ian as it was very hands on and we were just so enraptured with it. Neil had a clay mould ready to go which was heated in a kiln, whilst bronze ingots were melted in the furnace with Ian controlling the temp, once the bronze was melted and the clay mould at the right temp it was packed into a tube with sand vertically to compress the clay and stop any breakages. The bronze was poured into the mould, then five minutes later we took it down to the loch and cooled it down with the Tay and let the mould crack off the blade. It was just such a magical process; the seven on us just stood there in silence, looking at it reverently for a very long time.
Then we were given a blade blank each that Neil had masterfully cast (it would have taken far too long to cast a blade each on the course, considering success/fail rates) and got to work shaping the edges and polishing them up. We did as much as we could in the time, and will hammer harded the edges with Neil at a later date and make our own handles and scabbard. Neil also demonstrated and talked us through the evolution of the bronze sword with different ways they were cast and his research into how to recreate them it was astounding the skill and time involved in such a process.
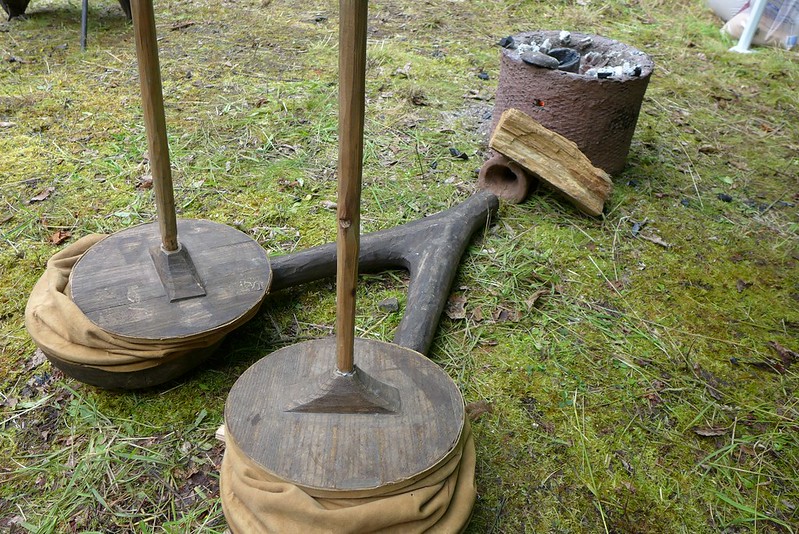
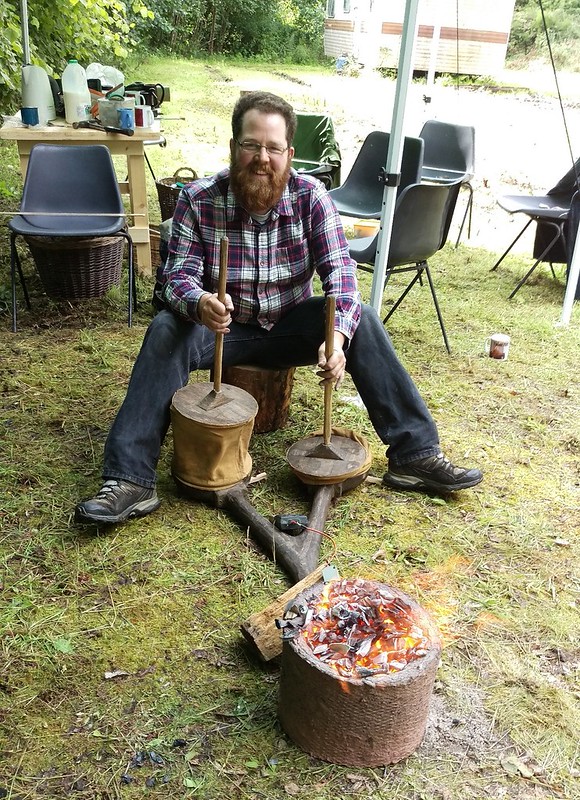
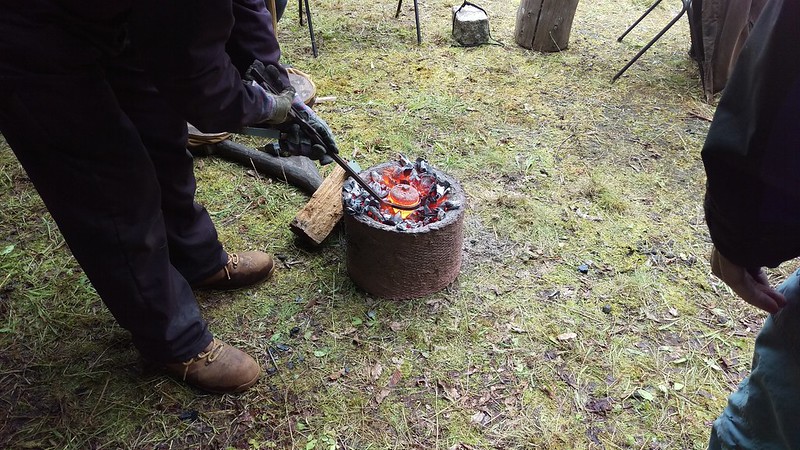
Pouring the molten bronze into the mould.

Cooling the sword in the Tay.
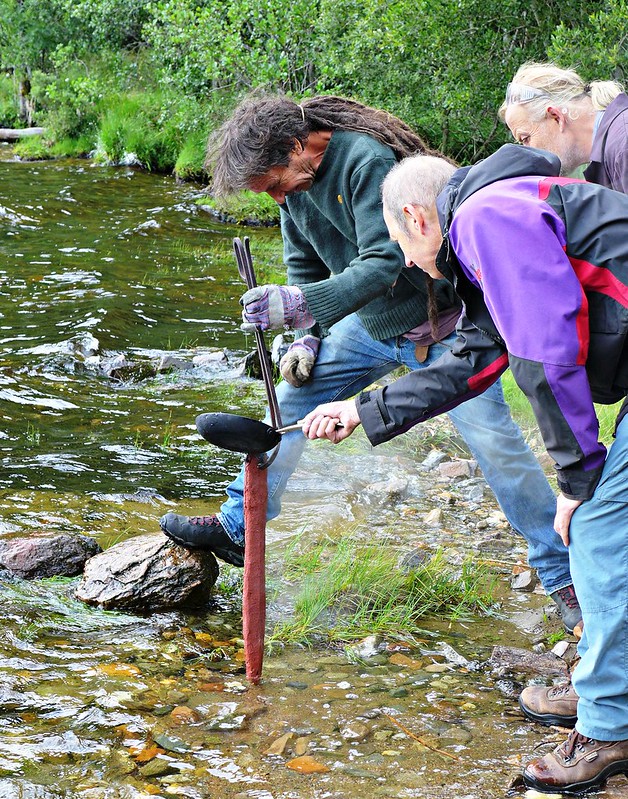
you can see the mould breaking away from the blade now
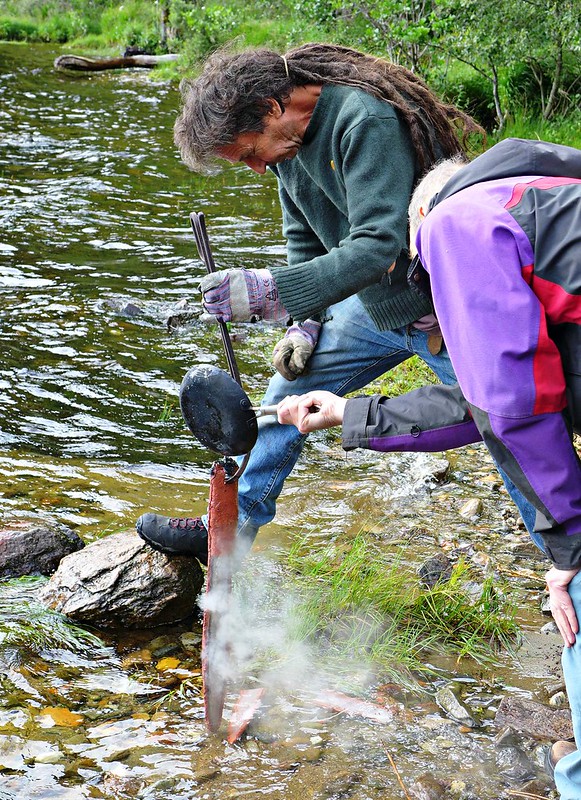
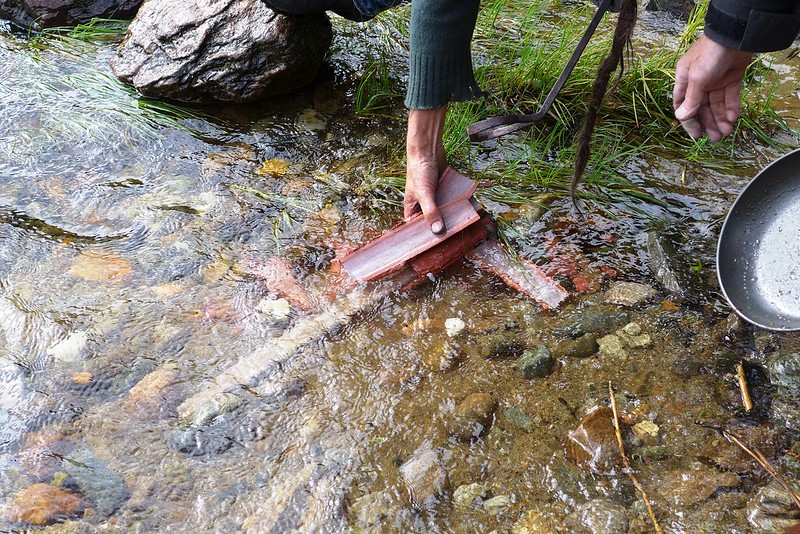
in quiet reverence of this magical art
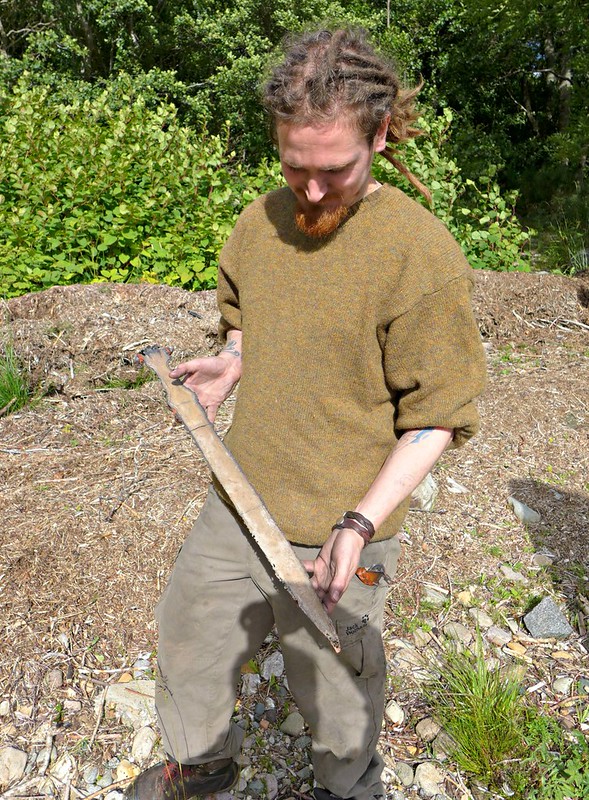
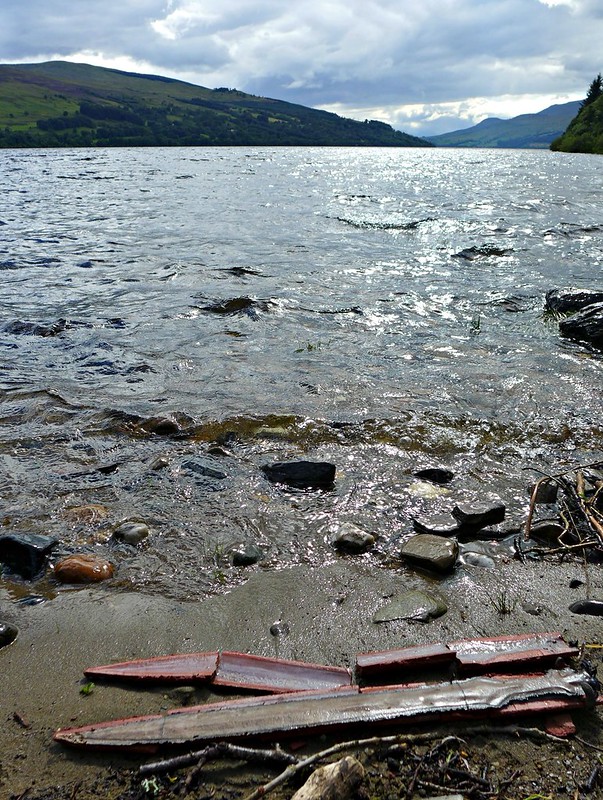
The newly cast sword next to one of Neils finished swords.
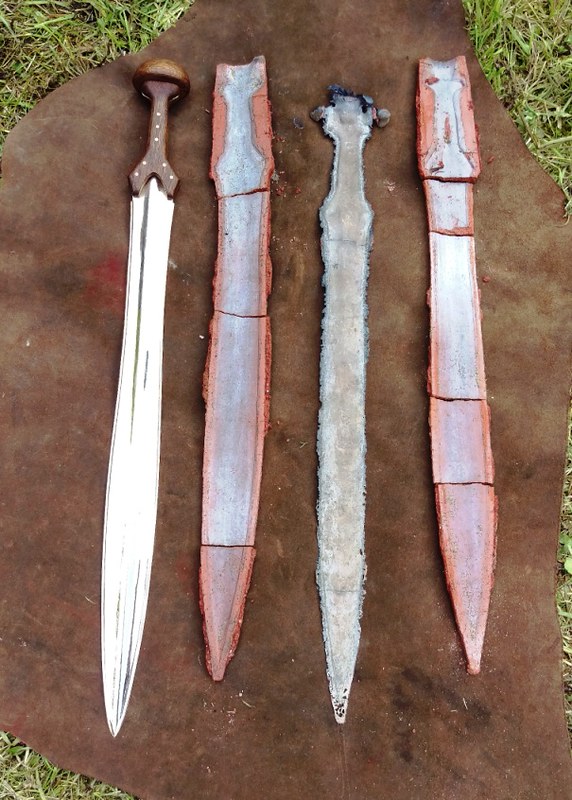
Whilst polishing our swords, Neil asked if we wanted to have a bit of fun and experiment with one of his other blanks. Bronze swords need to be sort of 'tuned' for battle. Due to the material, when struck they will bend slightly. Being double edges, you can strike several times, flip the blade then strike with the other edge and it will straighten itself back out. Each time the blade is struck, the material hardens up so after a time it should stop bending. We decided to test this out by anchoring a sword and whacking it with a thick peice of timber. It was whacked twice, flipped, and repeated at least 40 times. at the beginning the sword would bend a little, but eventually it had straightened out and hardened. We all had a bit of fun chopping up a log and felling a tree with a rough cast sword for larks. It really brings to light what a bronze sword can do to soft water filled meat sacks like us.
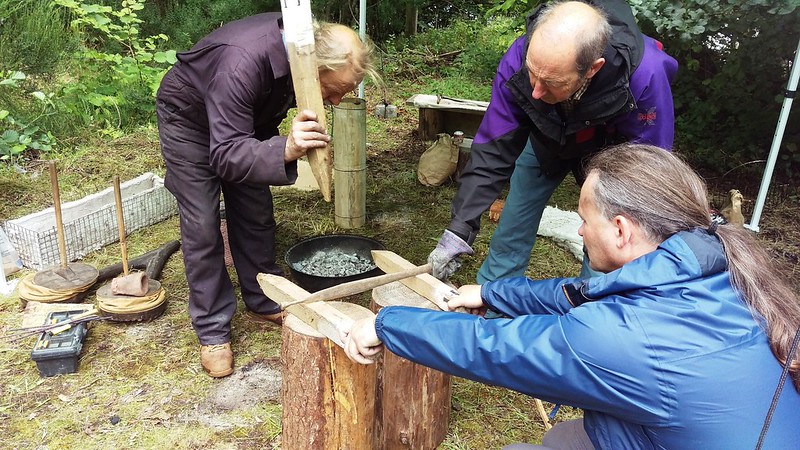
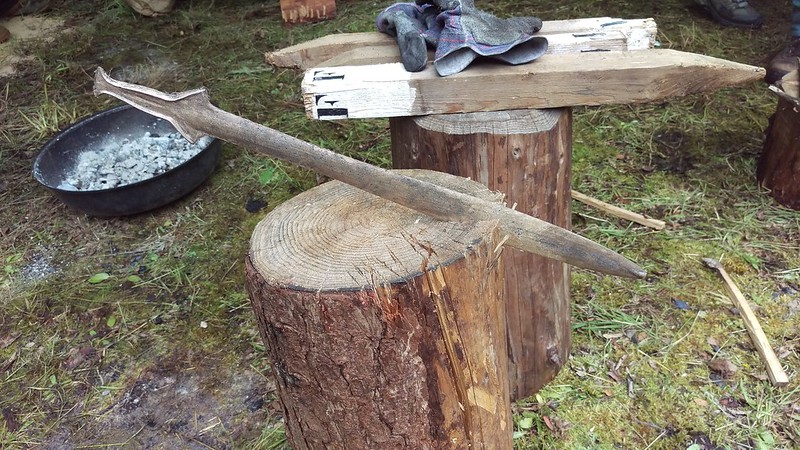
An unpolished sword straight from the cast next to a semi polished one. The bronze really wants to shine through
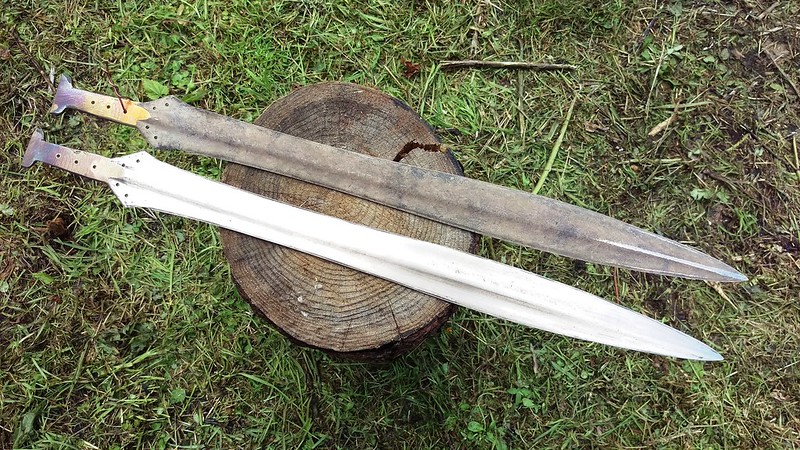
Happy students
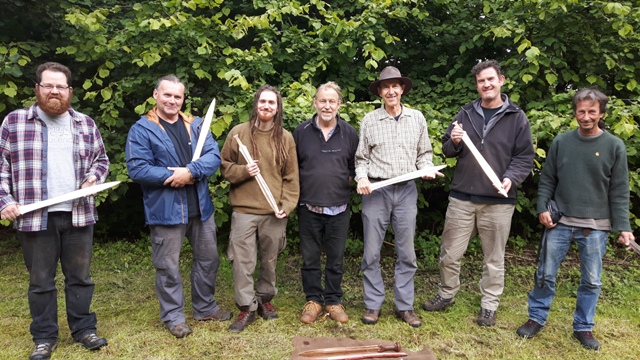
It's amazing just how much skill goes into making a bronze sword, form the research into structure, heat, materials, to making the moulds, getting the casting right, then finishing them with hammering the edges without cracking the blade and even fitting the handle and making the scabbard. I just can't wait to get my sword finished now!
Thanks for reading my gibberish. Lets all go play with sharp pointy things in the woods...
Beezer of this parish came up with me to help out as my assistant on my stall, and then we both stayed on for an extra two days to attend Neils bronze sword workshop where we all cast a sword together, then were each given a pre master cast blank to work on as our own.
The Crannog
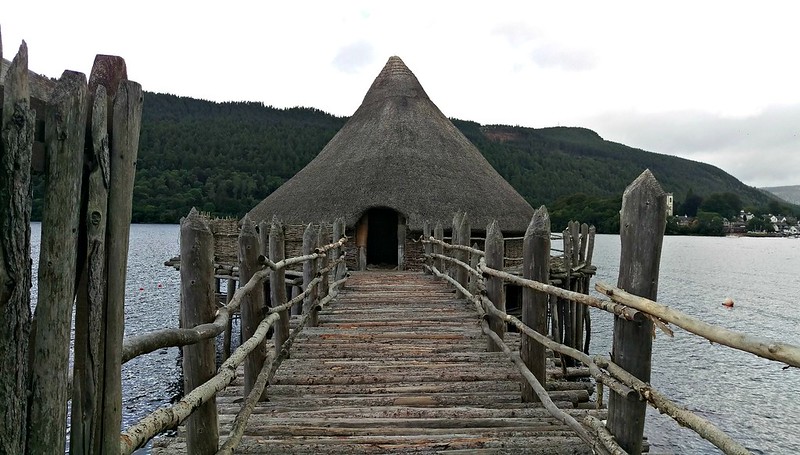
Stall
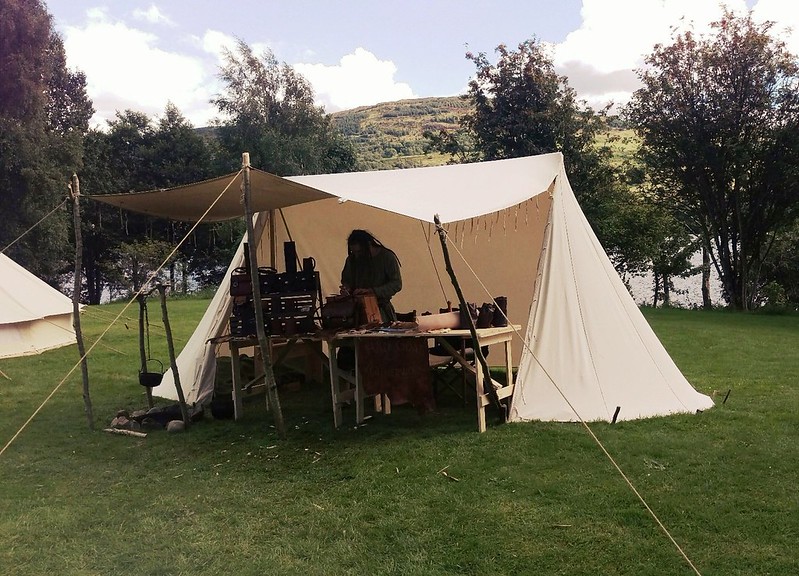
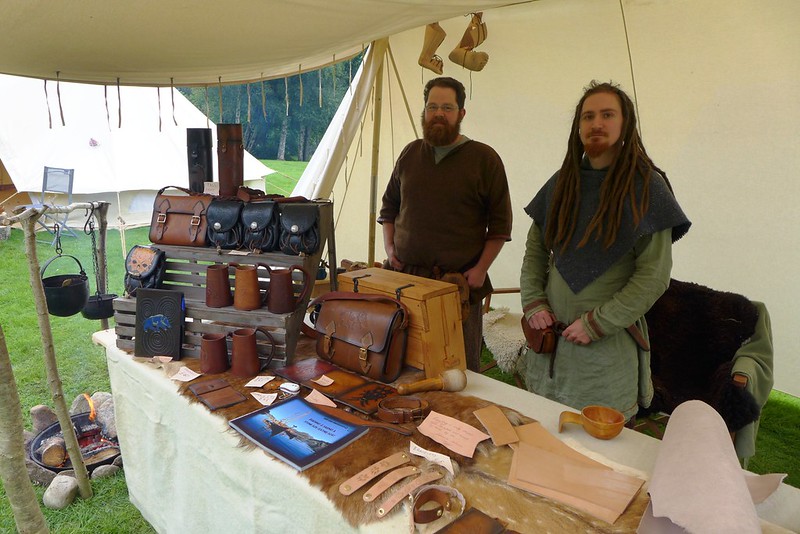
Log Boat
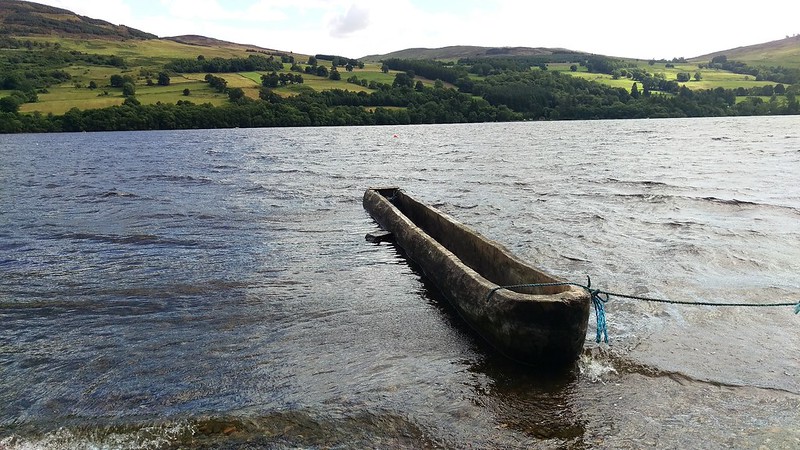

On to the bronze sword workshop. Only got a few pictures quickly snapped by me or Ian as it was very hands on and we were just so enraptured with it. Neil had a clay mould ready to go which was heated in a kiln, whilst bronze ingots were melted in the furnace with Ian controlling the temp, once the bronze was melted and the clay mould at the right temp it was packed into a tube with sand vertically to compress the clay and stop any breakages. The bronze was poured into the mould, then five minutes later we took it down to the loch and cooled it down with the Tay and let the mould crack off the blade. It was just such a magical process; the seven on us just stood there in silence, looking at it reverently for a very long time.
Then we were given a blade blank each that Neil had masterfully cast (it would have taken far too long to cast a blade each on the course, considering success/fail rates) and got to work shaping the edges and polishing them up. We did as much as we could in the time, and will hammer harded the edges with Neil at a later date and make our own handles and scabbard. Neil also demonstrated and talked us through the evolution of the bronze sword with different ways they were cast and his research into how to recreate them it was astounding the skill and time involved in such a process.
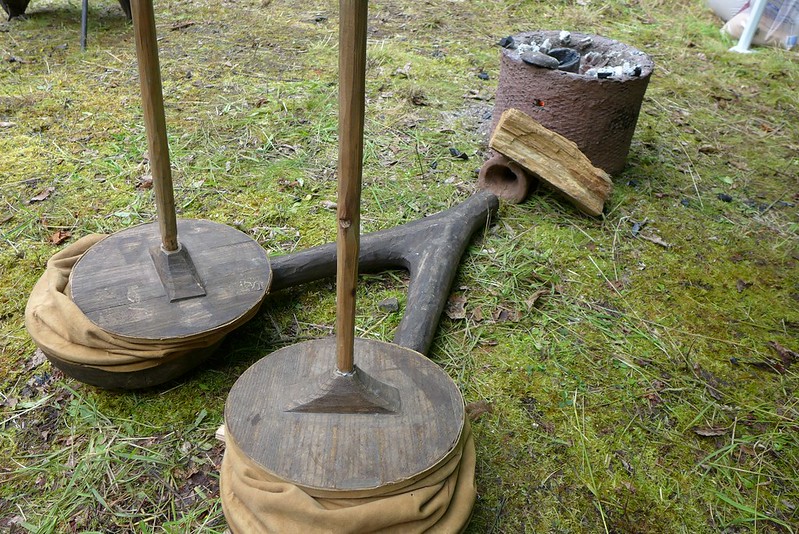
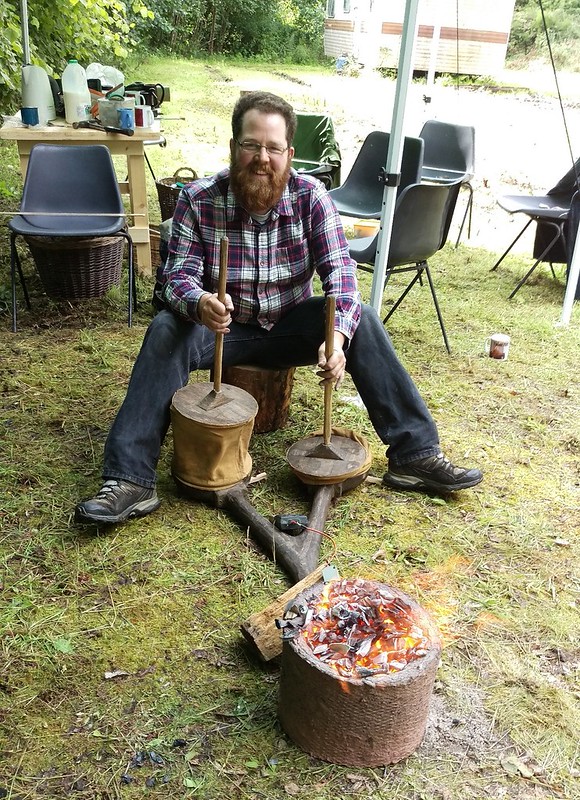
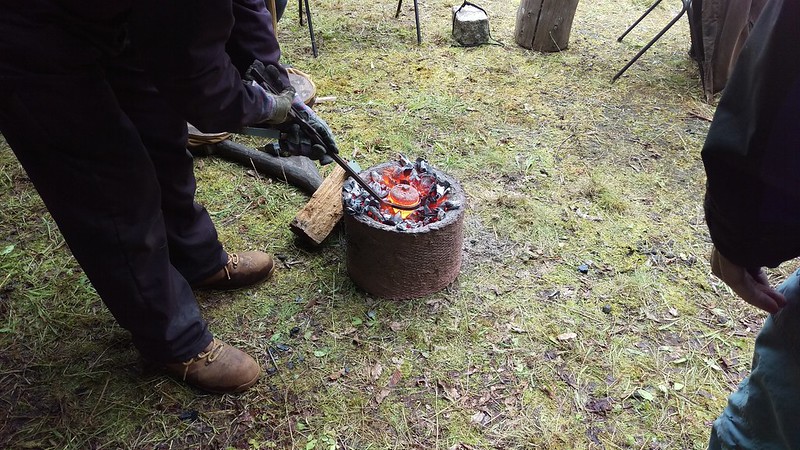
Pouring the molten bronze into the mould.

Cooling the sword in the Tay.
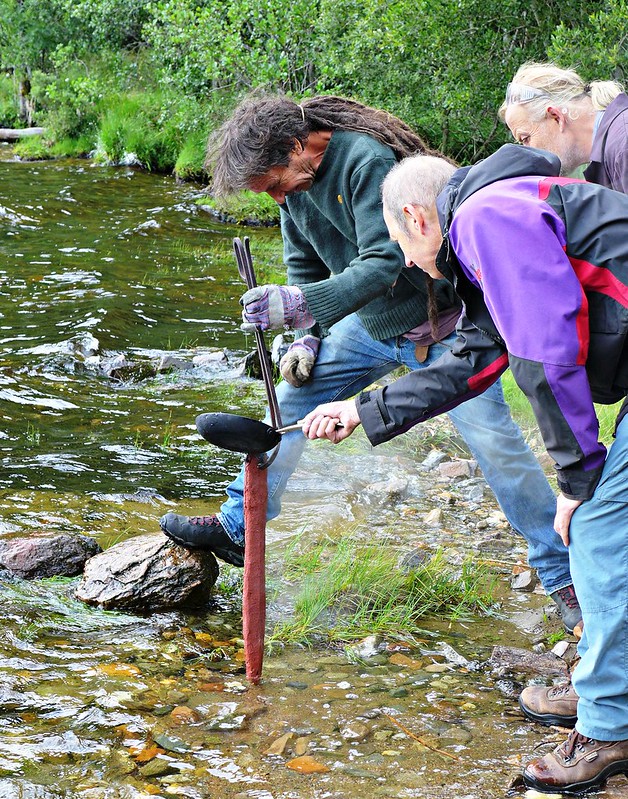
you can see the mould breaking away from the blade now
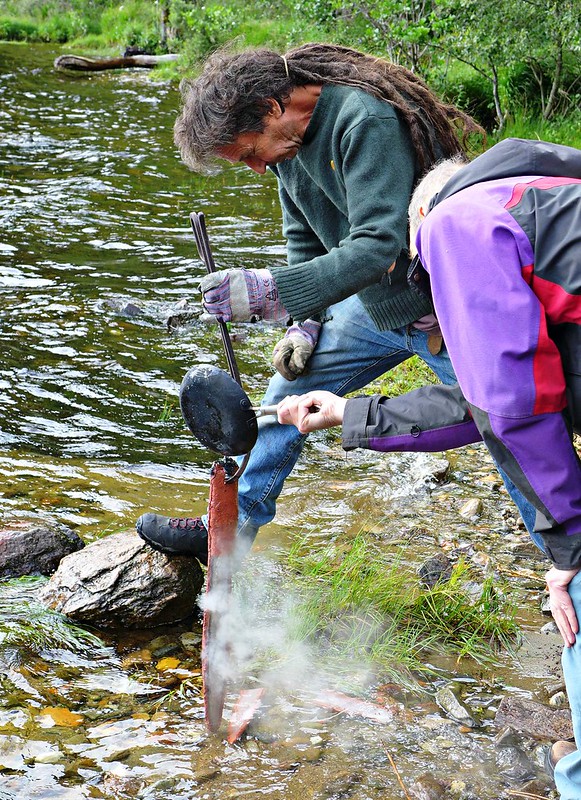
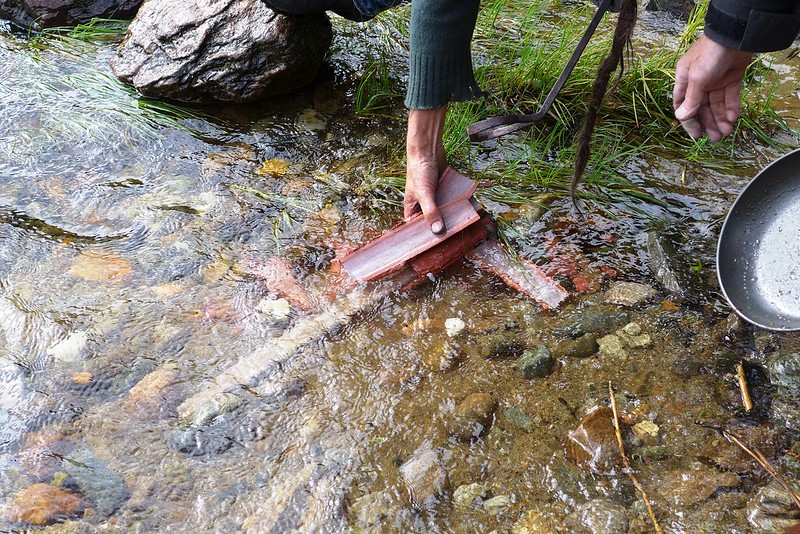
in quiet reverence of this magical art
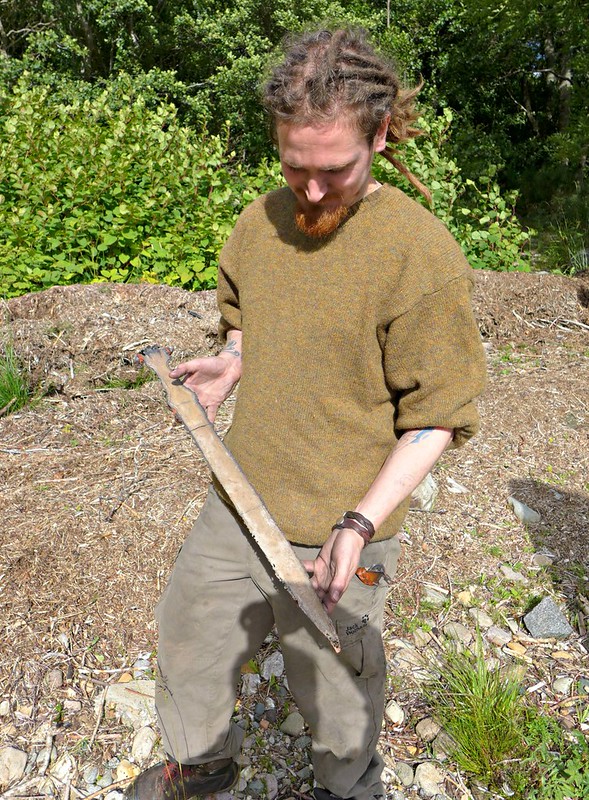
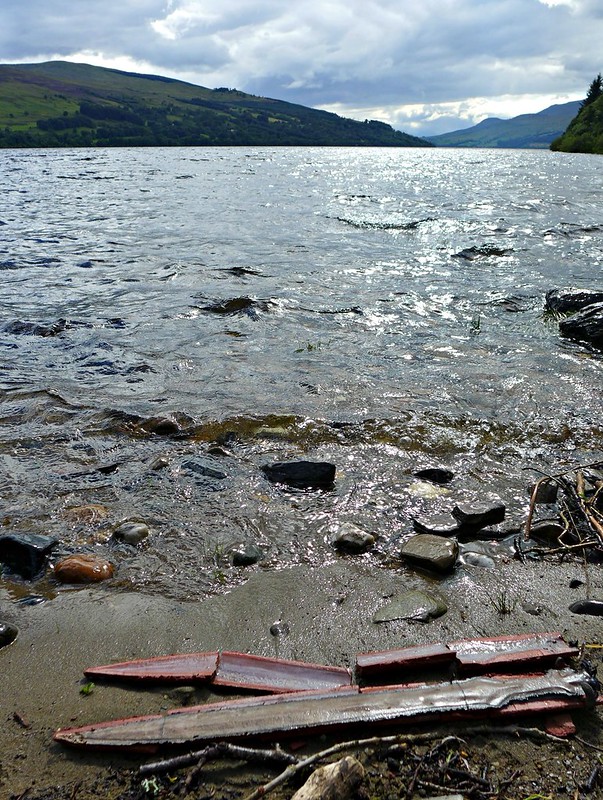
The newly cast sword next to one of Neils finished swords.
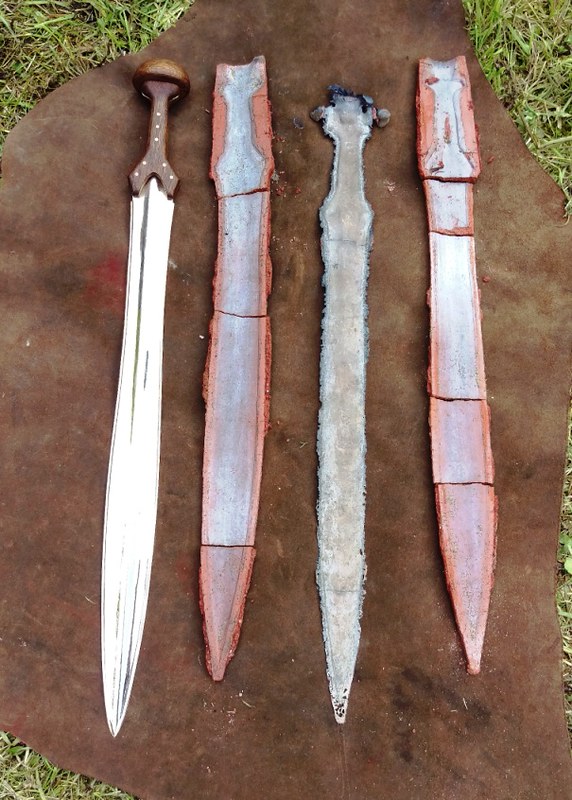
Whilst polishing our swords, Neil asked if we wanted to have a bit of fun and experiment with one of his other blanks. Bronze swords need to be sort of 'tuned' for battle. Due to the material, when struck they will bend slightly. Being double edges, you can strike several times, flip the blade then strike with the other edge and it will straighten itself back out. Each time the blade is struck, the material hardens up so after a time it should stop bending. We decided to test this out by anchoring a sword and whacking it with a thick peice of timber. It was whacked twice, flipped, and repeated at least 40 times. at the beginning the sword would bend a little, but eventually it had straightened out and hardened. We all had a bit of fun chopping up a log and felling a tree with a rough cast sword for larks. It really brings to light what a bronze sword can do to soft water filled meat sacks like us.
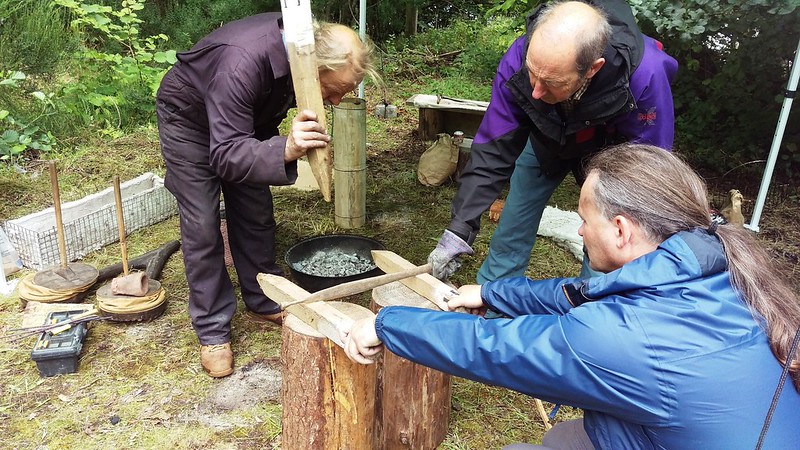
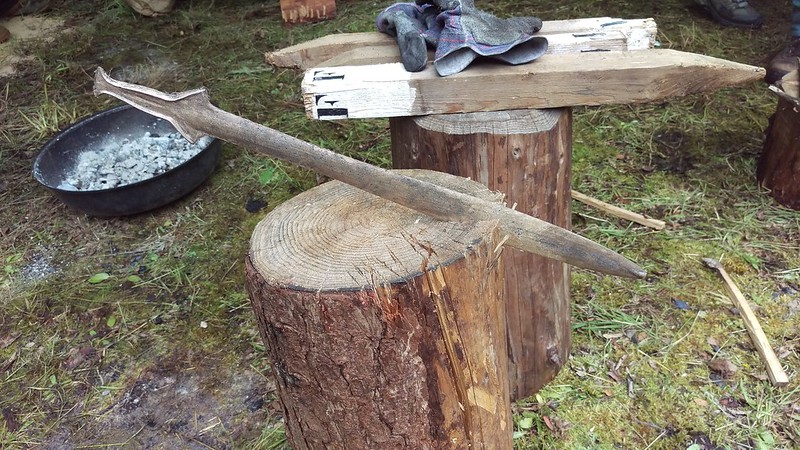
An unpolished sword straight from the cast next to a semi polished one. The bronze really wants to shine through
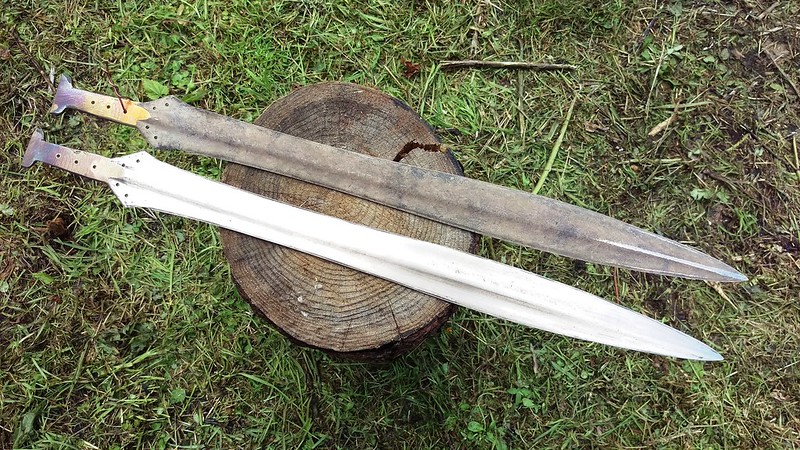
Happy students
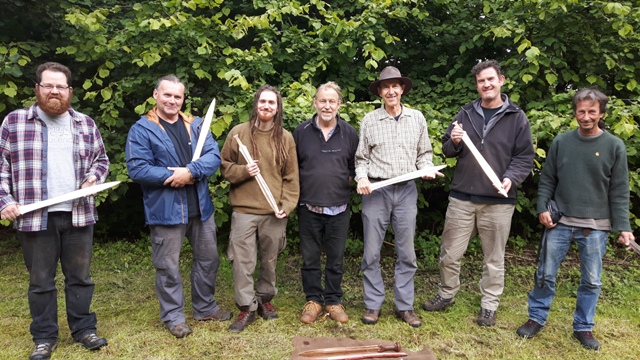
It's amazing just how much skill goes into making a bronze sword, form the research into structure, heat, materials, to making the moulds, getting the casting right, then finishing them with hammering the edges without cracking the blade and even fitting the handle and making the scabbard. I just can't wait to get my sword finished now!
Thanks for reading my gibberish. Lets all go play with sharp pointy things in the woods...