Got an old saw? Put it to use as new knives!
This is a simple project that was inspired by a chance encounter with a young lad named Woody at the last summer Moot.
Apparently whilst the rest of the family was setting up camp, Woody found (amongst other treasures) a discarded handsaw of the cheap plastic handle variety. Later in the week Woody and his dad asked me if I could make a knife from it; so I made Woody and his siblings a knife each using nothing more than a cordless angle grinder and a file.
Find an old saw
Hobby knifemakers often turn large circular saw blades and industrial bandsaw blades into knives, but even cheap handsaws will make decent enough knives. They are spring steel and if you feel so inclined, you could re-heat treat them to be harder, but in their off-the-shelf state, they will still hold an edge. It will never hold the same edge as your super-hard high-spec knife steels and will need sharpening more often, but it is also easy to resharpen when you need to.
I just happened to have such a saw sitting in a pile of rust in a shed, as many of us do!
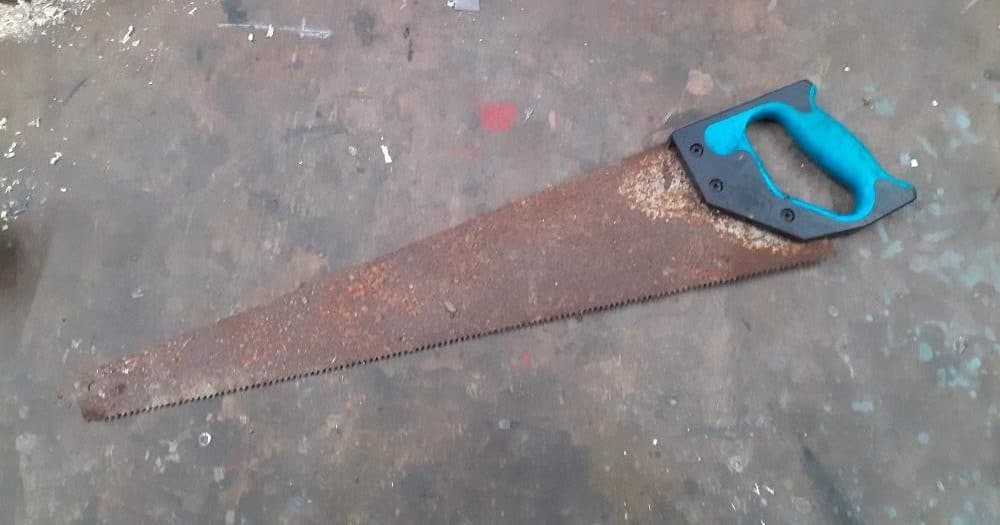
I started by removing the handle and sketching a few blades in chalk, being careful to avoid the teeth (which have been induction hardened and are way too hard to be useful).
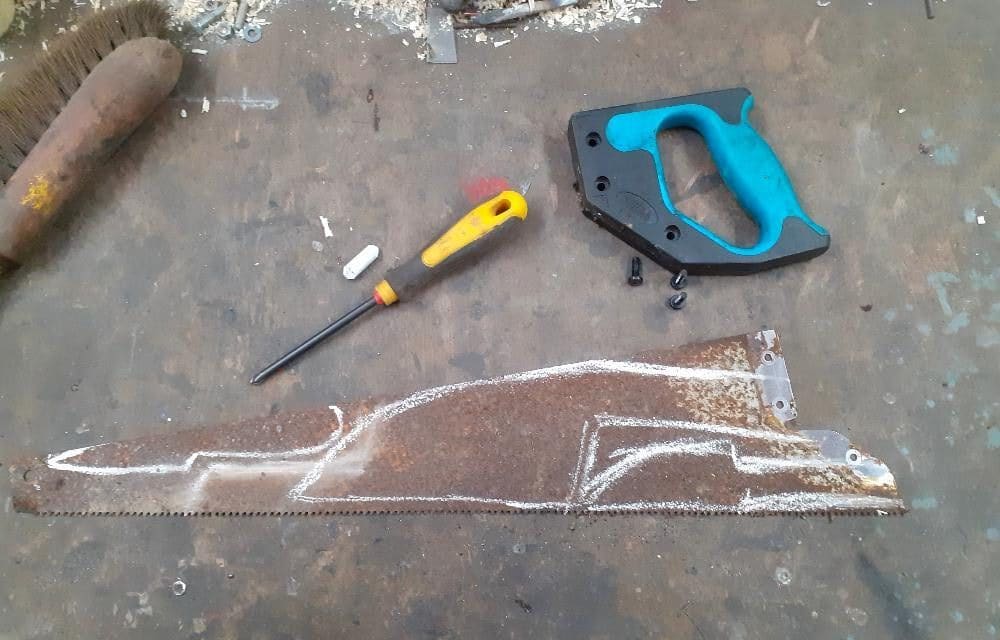
Shaping the knives
Heavy snips, bench shears, metal cutting bandsaw, a jigsaw or an angle grinder are all good choices for cutting these blades out
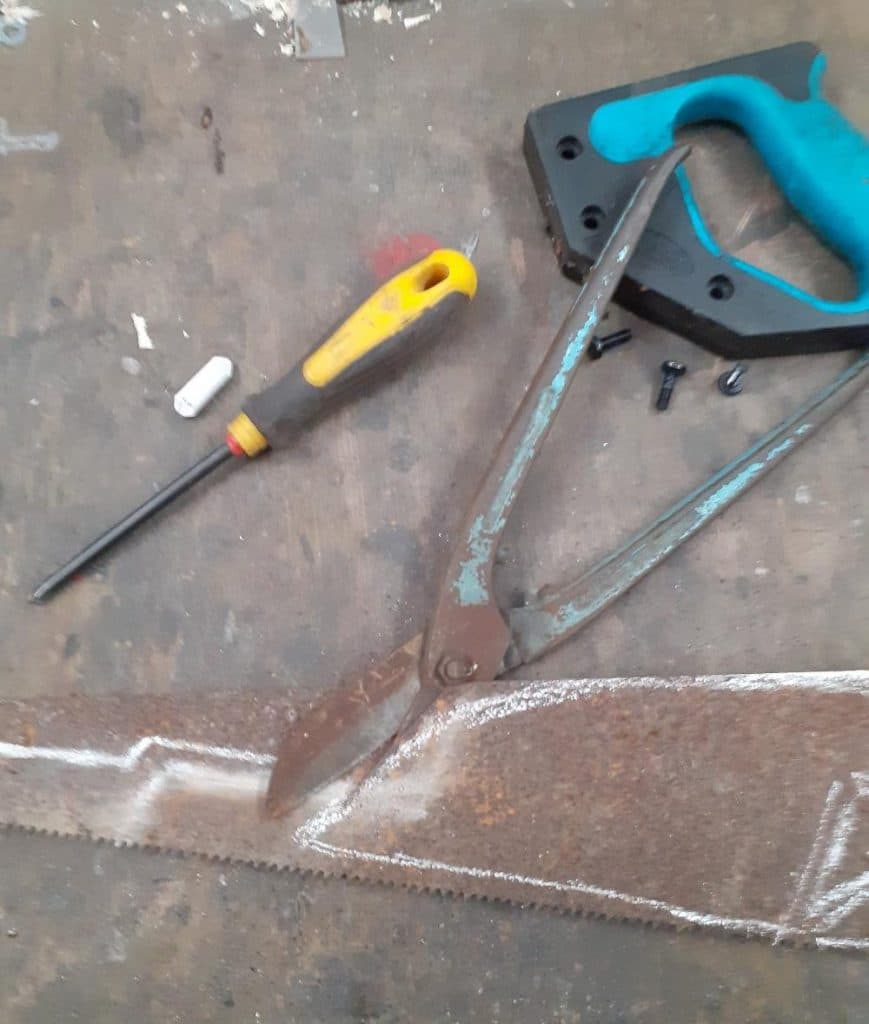
If using an angle grinder then thin slitting discs are the way to go. They generate less heat, so the amount of over-heated (and subsequently too soft) steel will be limited to only a couple of mm, as can be seen by the slightly darker outline to the centre blade in the picture.
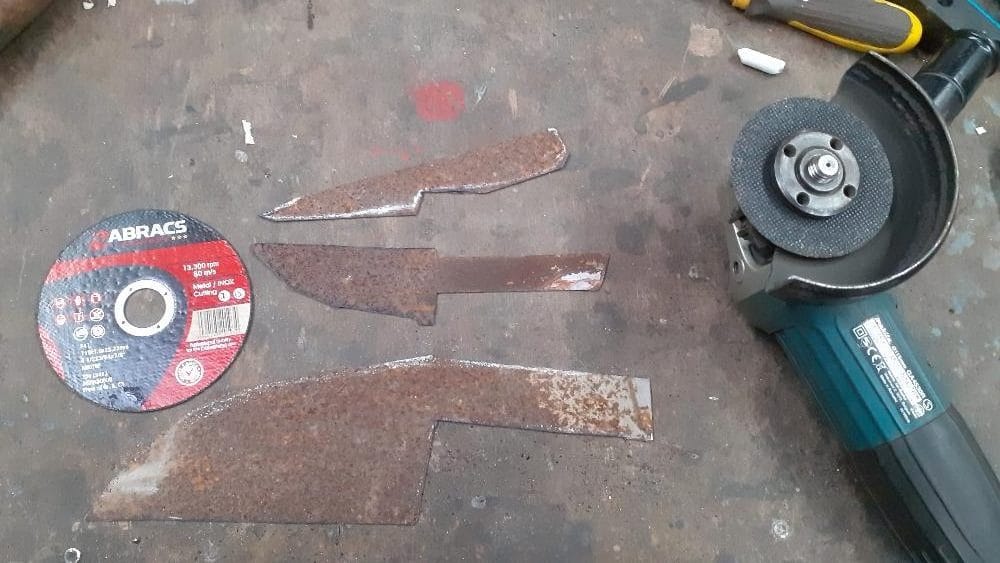
The shape of the blade can be refined using files or a grinder, again being careful not to overheat the blade. It is often useful to clean the blade back to shiny metal before any grinding so that you can see that you are not getting the metal too hot (if you see the metal change colour, then it was too hot).
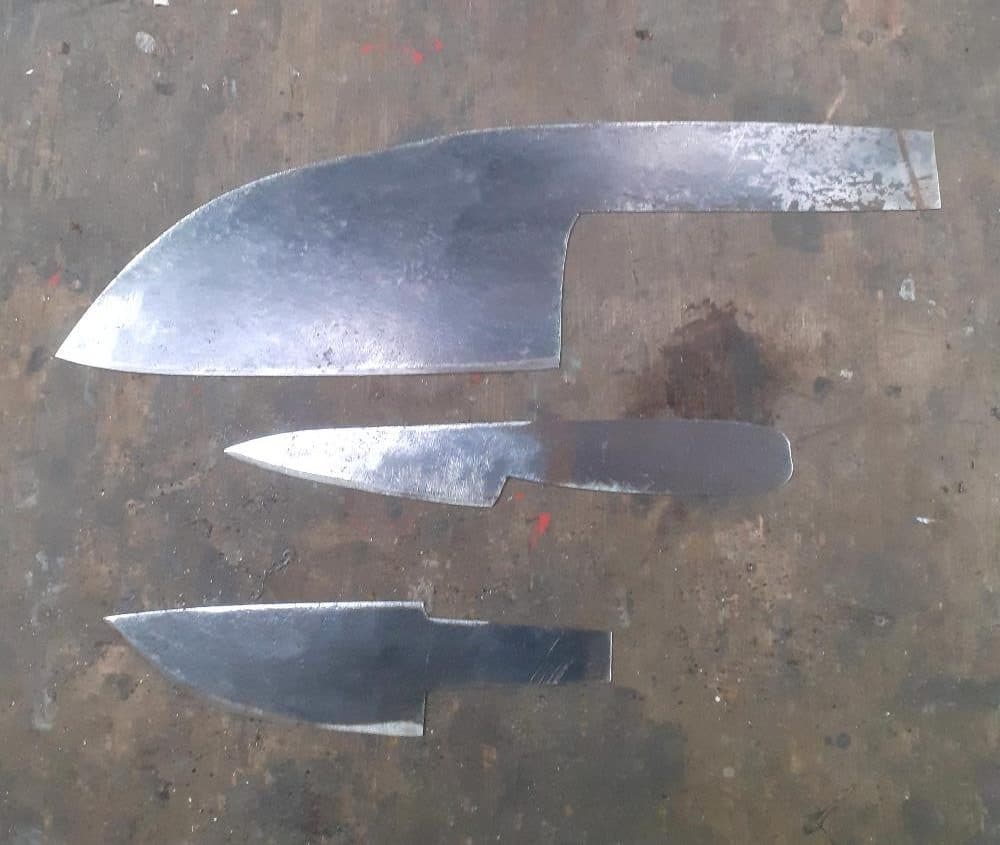
Putting the edge on
Since the blades are less than a millimetre thick, to begin with, the bevel grinding is more like sharpening. So I have ground/filed these to a shallow convex edge, which gives the edge added strength whilst still letting it cut very nicely.
At this stage, I have just taken the metal to a dull edge with the final bit being done after the handles are on and I am able to sharpen on a stone as normal.
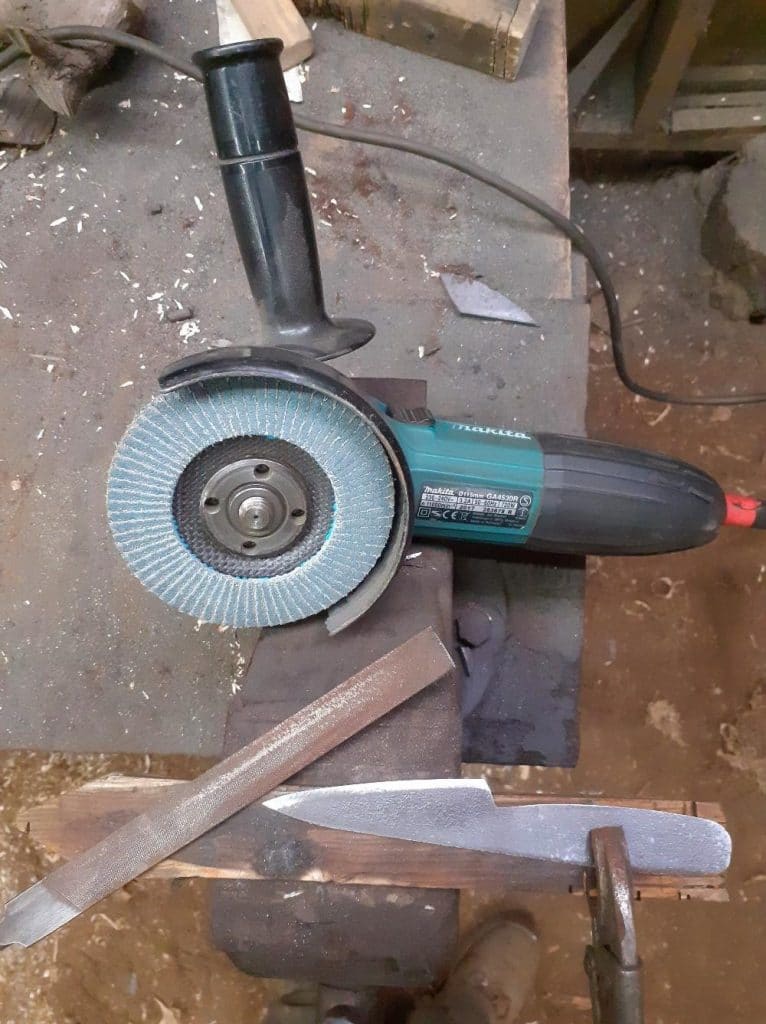
Since I was making these in a hurry (the 3 finished knives took about 2 hours) and with limited tooling, I went for zero-glue options that also work well with such thin and flexible stock.
Putting the handles on
The first (and simplest) method is how I made Woody’s knife. The handle was bound in a bit of string to add bulk and then good old gaffer tape to finish the handle off. Quick and dirty, but a very effective handle! Great for small general-purpose knives like this.
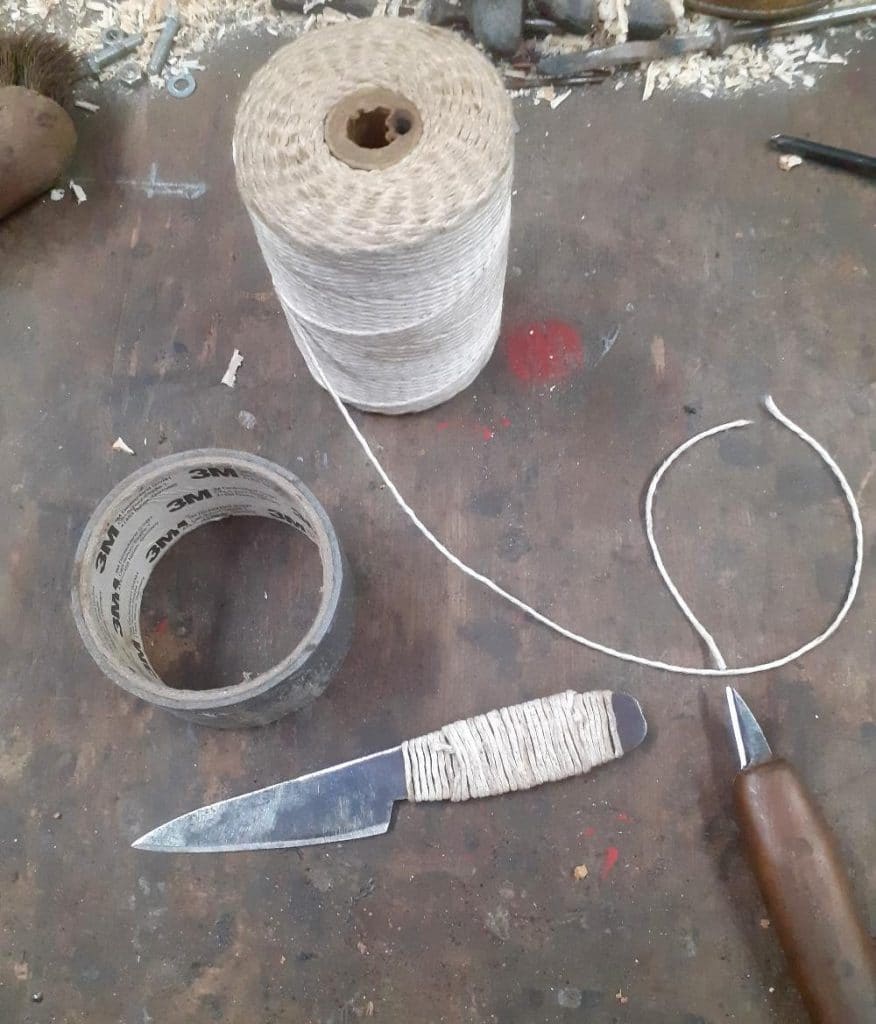
The second handle is your classic full tang knife, but done fast and in a historical fashion. A bit of hazel (seasoned in this case) is split and then planed/sanded/carved to have flattish mating surfaces.
The wood and metal are held together (I used a bit of tape to help) and drilled through with my drill press, though holes could’ve been punched in the metal with a nail punch and hand drilled through the wood.
A couple of 2” nails and M3 washers are used to rivet the handle together and the knife is complete. I went for a wide bladed knife to allow me to make a kitchen knife that wasn’t too flexible despite the long edge.
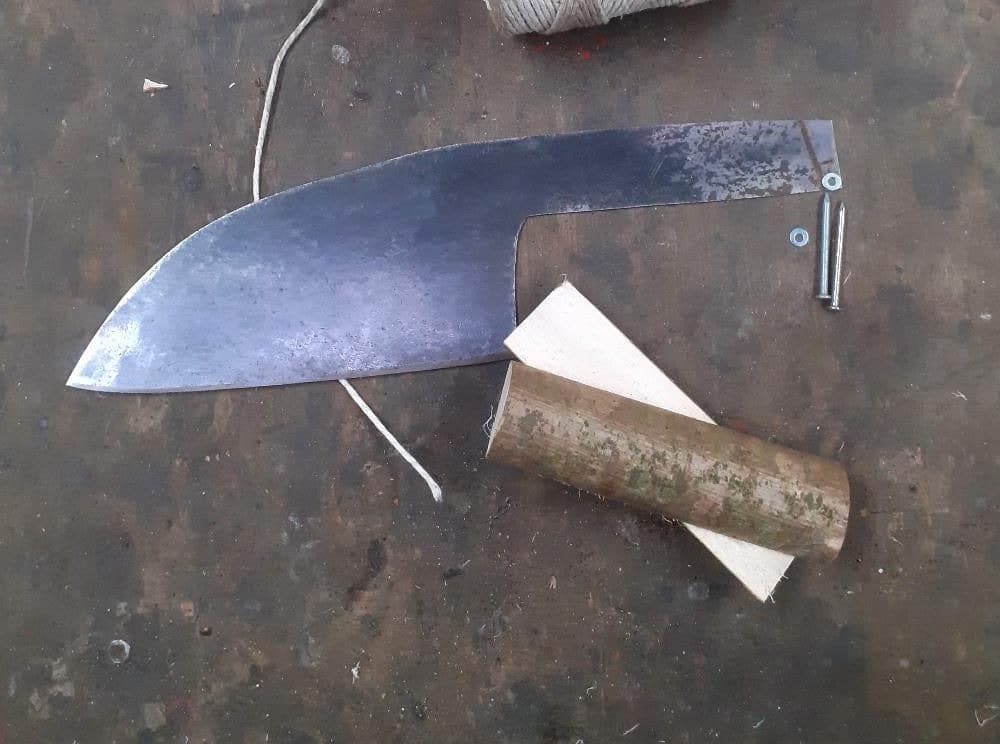
Finally the most complex but also my favourite method for handling such a thin bit of metal, this is how I make many of my historic handsaws.
A piece of hazel (seasoned again) has a slot is sawn to the length of the tang and the end is carved down so that it fits into a section of copper pipe. The blade is inserted; clamped in a vice and the handle driven on if needs be. A hole drilled through towards the end of the tang and a nail put through and peened (no washer in this case) to hold everything together. Another great general purpose knife.
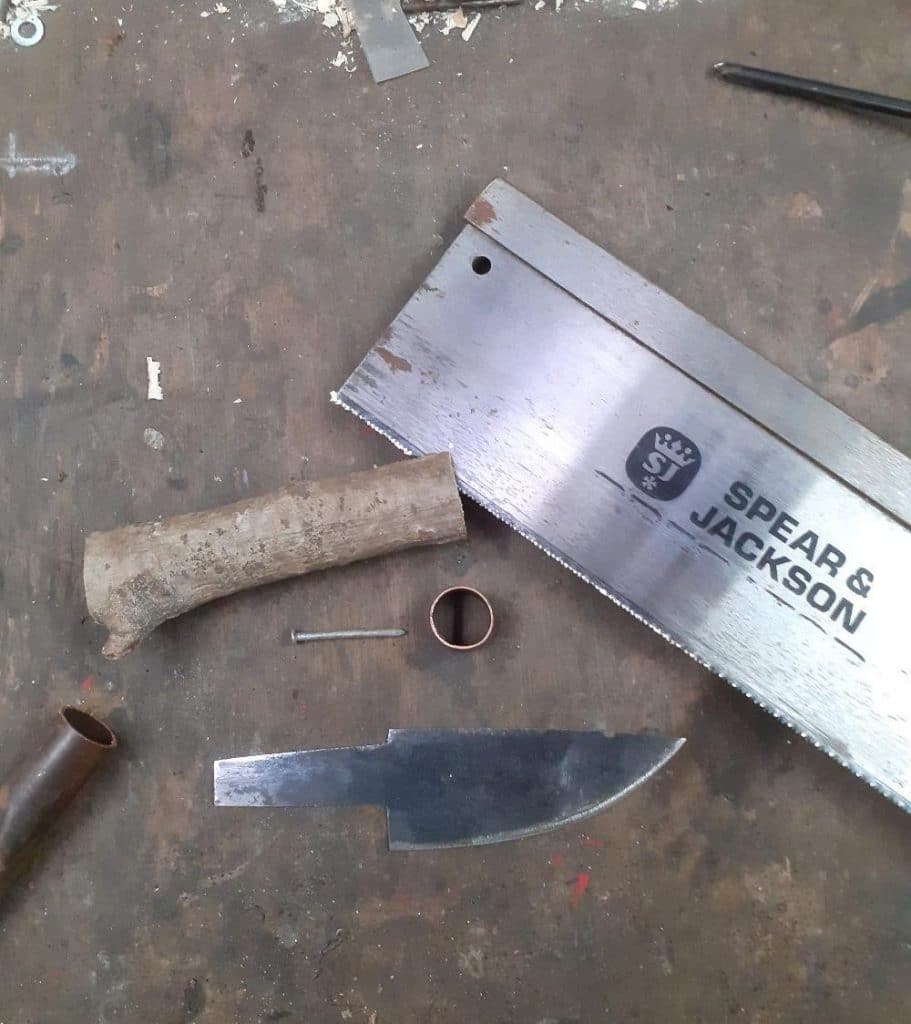
With the handles all fitted, I sharpened the knives on a stone as I would any other knife.
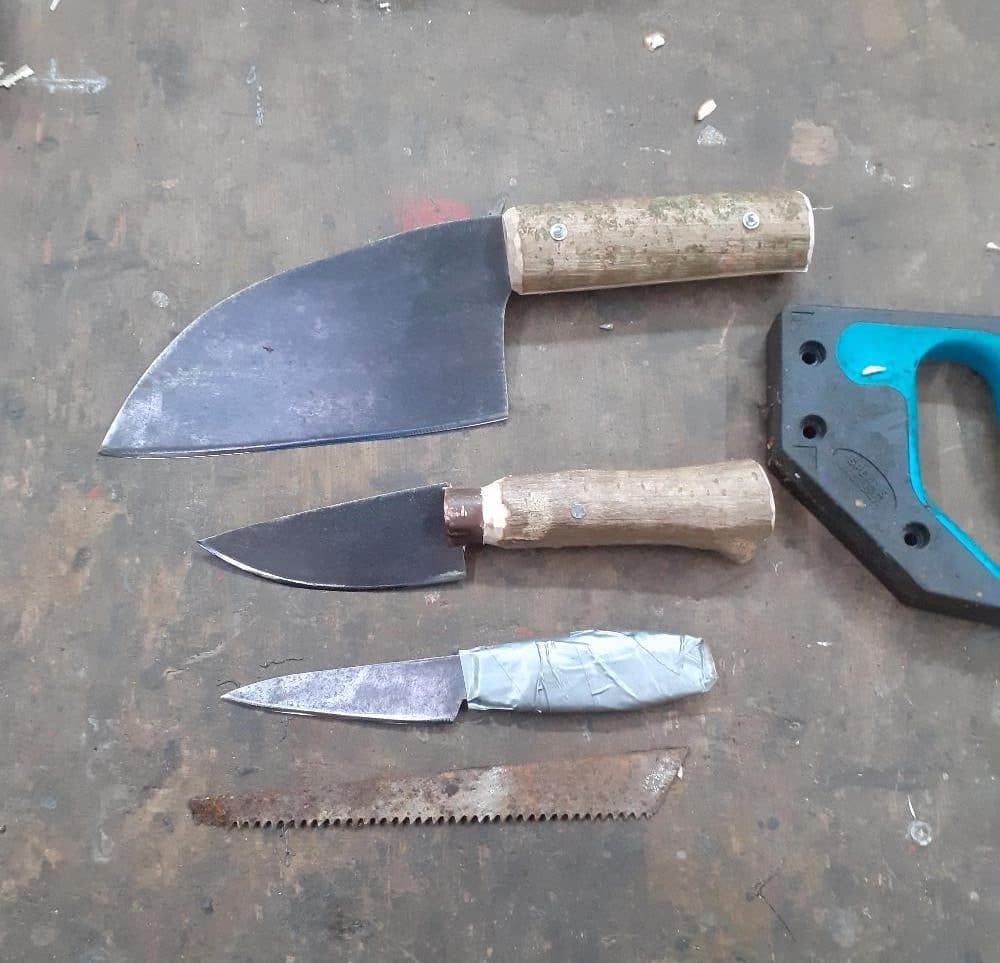
All done!
Not the prettiest or most robust knives that I have ever made. These are however plenty good enough for most things that bushcrafters actually use their knives for and cost nothing more than a little time and the junk we all have in the shed!
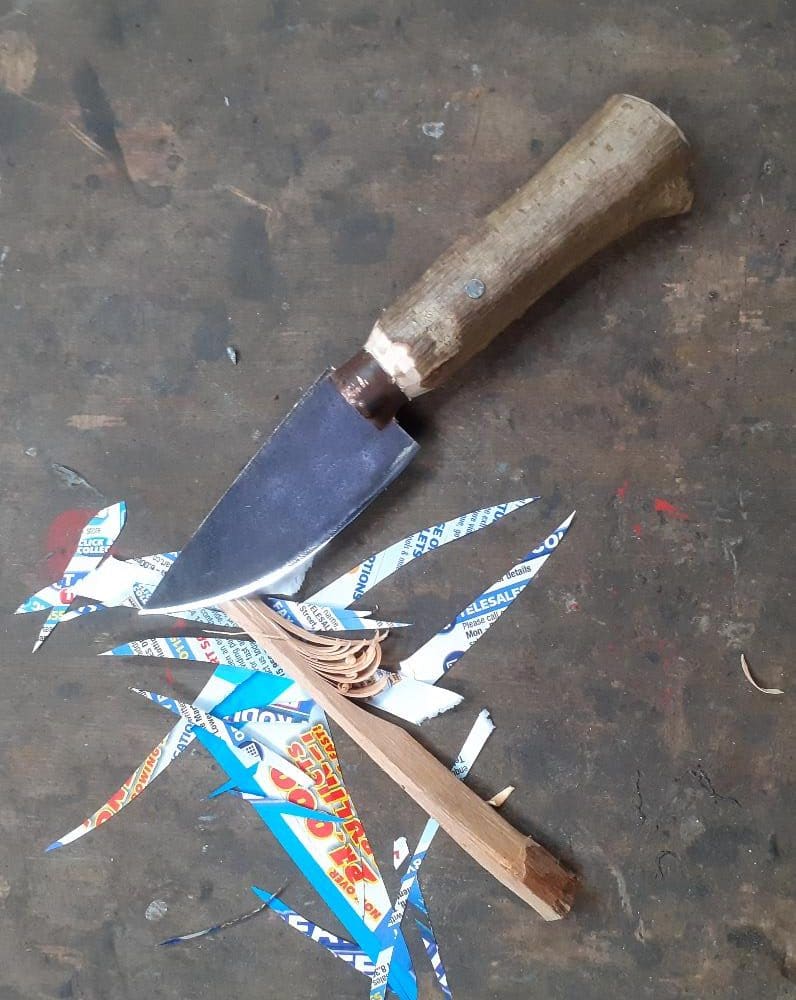
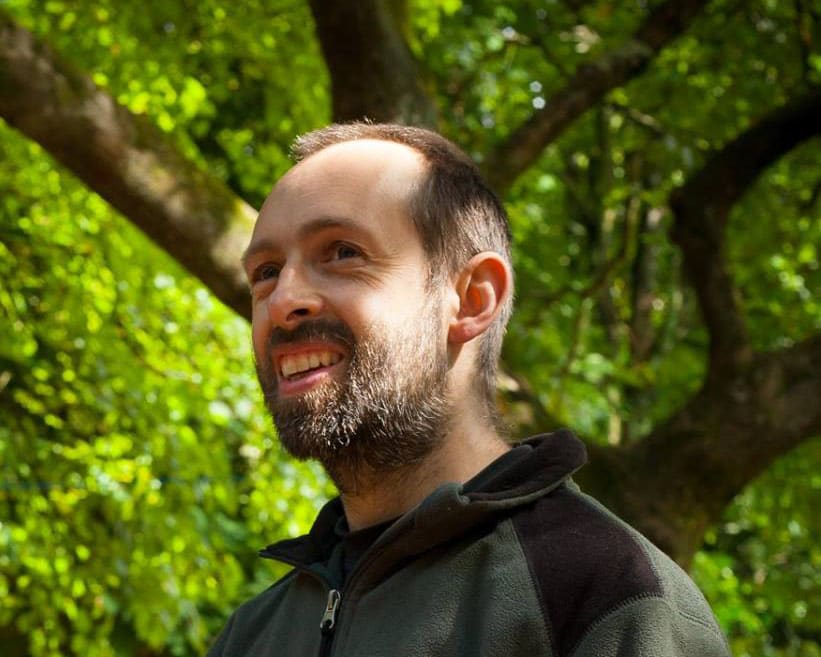
Dave Budd is a world renowned smith specialising in historic weapons and other period steelwork, he runs knife and axe making courses amongst other things from his woodland in rural Devon.
You can see some of his work and contact him through his website DaveBudd.com
Leave A Comment
You must be logged in to post a comment.