Another pretty obvious source of good steel for knives is the humble file. Most files are made from high-carbon tool steel and can be used to make great cutting tools.
That said, sometimes you will find a file that is just case hardened (i.e. only the surface/teeth will be high carbon, and the core will be soft mild steel).
The easiest way to find out which file you have is to put it in a vice with a couple of inches sticking out and smack it with a hammer. I recommend wrapping some tape around it first to catch the pieces and reduce the risk of shrapnel wounds though!
If the file snaps off cleanly, you have a winner, but if it bends, throw it away. It’s also worth noting that you should do this with the working end of the file and not the tang, as that is often left soft and would bend either way.
Most people will source their old files from car boot sales or other rusty tools in a forgotten toolbox or shed. If you can make out the maker’s name, then you will quickly learn good brands to choose for both stock material and actual use (though I would never buy a second-hand file because they are, at best, half dead to begin with). Some of the most common good files out there (in the UK) are Vallorbe, Grobet, Nicholson, Bacho, Oregon and Sandvik. I mostly buy Vallorbe files, so that is what I would be recycling.
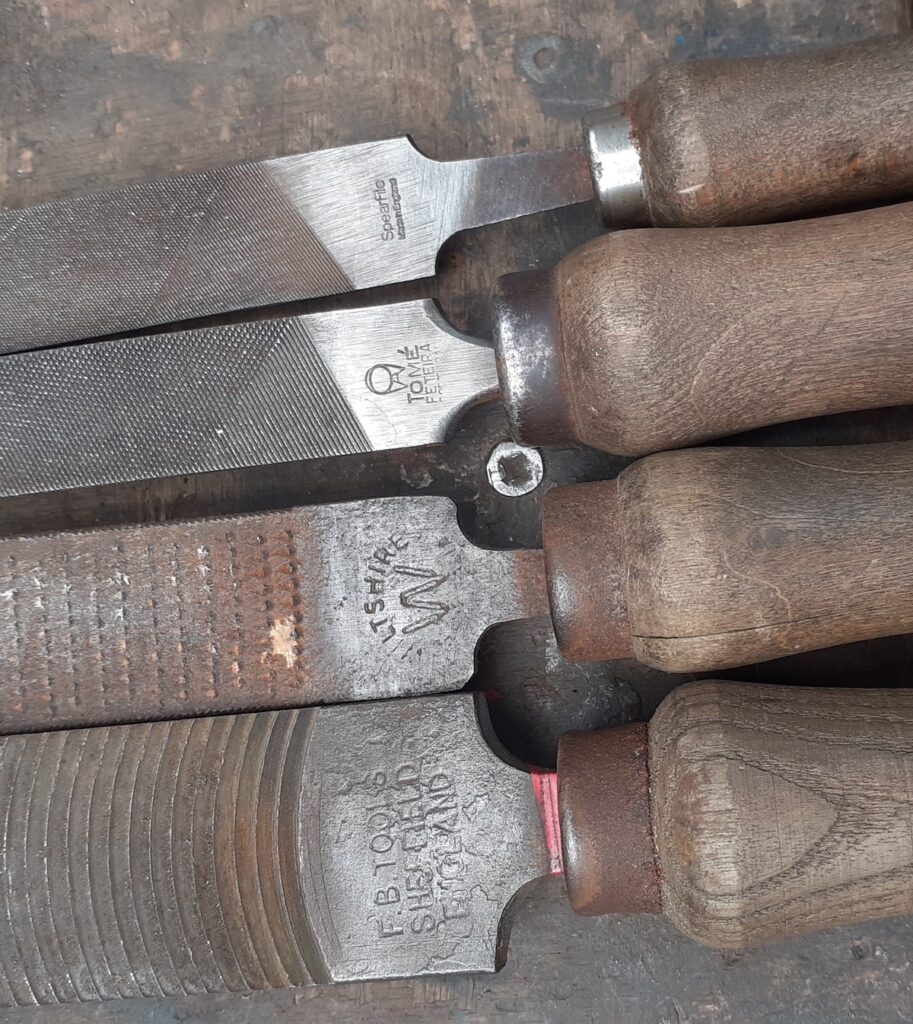
Assuming that you have a suitable file, you will need to decide how you are going to shape it into a knife: Forging, normal stock removal and careful stock removal.
Forging is the most versatile method and makes the most of the available material.
When forging old files, there is no need to anneal them first but be sure to remove the original hardness before forging to make sure the tang end doesn’t break off whilst you forge the hot end (just pass the file through the fire and heat each portion to dull red).
It is also a good idea to grind off any teeth that will fall near the cutting edge, especially on rasps and coarse files with very large teeth. If you just forge them into the edge, then you will get ‘cold shuts’ that can act as stress points and are likely to be the focus of cracks later on.
Generally speaking, files are very high carbon steel (over 1%), and you will need to avoid overheating them whilst forging. Try and stay in the reds and oranges; if you go to a very bright orange or yellow, there is a very good chance that it will turn to cheese and fall apart under the hammer!
The shape of the file doesn’t matter, either. For example, I’ve made some nifty looking knives from round chainsaw files; just flatten the blade portion and the rest can be coiled up, turned into a snake or tied in a knot!
Stock removal is the best way to maintain the original character of the file and not damage the teeth. Of course, you are limited by the size of the starting stock, but most flat files of 8” and under make nice little knives (larger files get quite thick).
If you are limited to using hand tools to make a knife, you will need to anneal the file first. The easiest way to do this is to light a small campfire and stick the file in it to heat up. As long as it gets to a dull red, then the steel is normally OK to work on, but ideally you want to bring it to just beyond non-magnetic (mid-orange) and leave it to cool slowly, preferably buried in wood ash/sand/vermiculite.
If you have a forge or other heat-treating kit, use that instead; you will need to re-harden it later anyway. If you get it too hot or very uneven, then you are likely to cause yourself problems with grain growth and possible air-hardening (burying it in an insulting material safeguards against air hardening) that will need to be dealt with later. Once the file has been annealed, you can treat it like any other piece of stock steel material.
Some of my first few knives were made from old files, and there is a perverse sense of pleasure in using a good file to file a file! You can drill it, file it or grind it with whatever tools you have to hand.
If you have access to a good grinder (a knifemaker’s belt grinder, for example) and are careful, then you can do all of the grinding in the as-hardened state. Often when I make files into knives, I do it this way. I simply temper the file to reduce it’s hardness to something suitable for a knife and then grind the bevels of the blade carefully, being sure to not over heat it and ruin the temper. This does take practice, but practice makes perfect!
Abrasives don’t really care if the steel is hardened or not, in fact, often hardened and tempered steel is easier to grind because it is less ‘gummy’ than annealed steel. The key is to use SHARP abrasives, not the dull belt that you should’ve thrown away a long time ago! A light touch, especially with the finer grits, is good. Still, I tend to lean into the coarse grits and let the SHARP abrasive do its job of cutting and not just rubbing away at the steel. Dipping the blade into water to cool when it gets warm and being careful when working near the edge or tip. I find this easy to do because I hold the blade in my hand and not a jig, where you can’t feel the heat being generated. If there is any bluing, then that area won’t hold an edge at all.
The tang area can have the temper drawn further by heating it with a torch until it forms a grey oxide on the surface. This further reduces the chance of snapping and allows you to drill holes for pins or lanyard.
Heat treating. As with all recycled material, this is always going to be a case of best guess and experimentation. The fact that I only buy Vallorbe/Grobbet and Oregon files means that I have worked out what works with them and can be more confident in the results than if I were to pick a random old file. That said, most files will be simple alloys and high carbon, so fairly simple heat treating that can be done at home without fine temperature controls. Aim for 800C (dull to mid-orange, just below non-magnetic) for the hardening and quench in thin, warmed oil. Many very old files were quenched in brine (file-making factories would transport their brine if they moved premises rather than try to replicate it), but if you choose to try this, I suggest reducing the temperature that you quench from to avoid warping or cracking. Temper to a full gold or straw for most knives, though brown will be OK; in real terms, look to 200-220C. Normal Vallorbe files, for example, retempered at 220C give a hardness of 60RC.
Of course, knives aren’t the only thing that old files can be turned into. I have several quickly made wood-turning tools made from them (just be sure to draw the temper from the non-working areas so they don’t shatter in your hands the first time you use them!). I’ve also got centre punches, wood carving chisels, metal cutting chisels, scrapers and a drawknife made from old files, as well as various impromptu specialist tools that get made mid-job and then put back in the file pile. I occasionally make files for living history, and the chisel I made to cut those teeth was made from an old file (only because it seemed appropriate).
Some years ago, I was fortunate enough to visit a fantastic tool museum in Troyes in France. Amongst their collection is a large display of tools made from old files and rasps. There are all manner of things in there, including billhooks, knives, axes, scissors, as well as those mentioned above. In addition to turning a file directly into another tool, they are a useful source of high-carbon steel if you are able to forge weld. A cutting edge of old file can easily be fire-welded into a mild steel axe head, a chisel can be re-steeled, a file can be laid between two bits of low carbon iron/mild to form a laminated blade for knives, etc, etc.
Oh, and files make great fire steels for striking flint against.
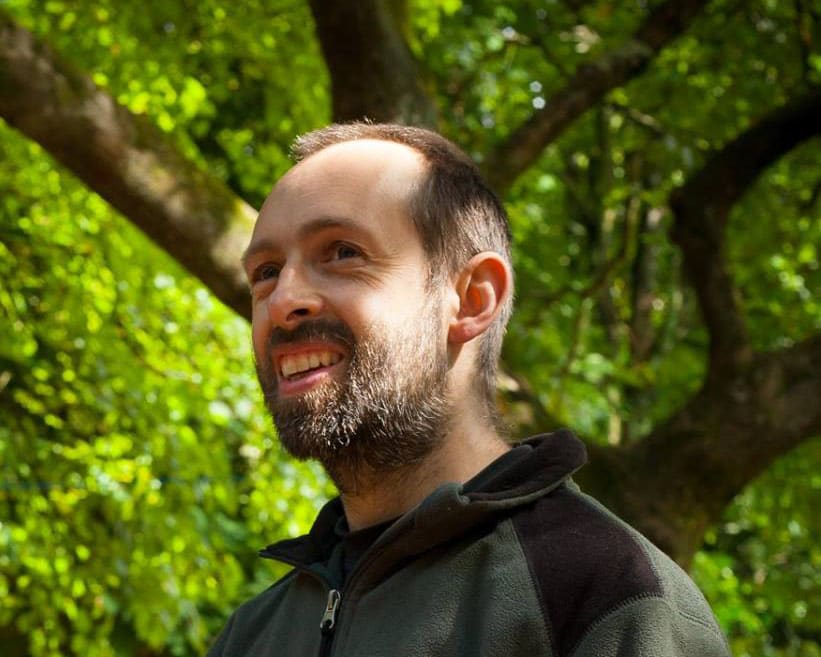
Dave Budd is a world-renowned smith, specialising in historic weapons, tools and other period steelwork, he runs knife and axe-making courses amongst other things from his woodland in rural Devon.
You can see some of his work and contact him through his website DaveBudd.com
Leave A Comment
You must be logged in to post a comment.