Ok, so it's not very bushcrafty; but I thought you guys (and gals) might be able to help all the same. I'm building a 4x2.5m shed (or hope to!), and just getting the order for the wood all sorted and want to make sure I have planned it correctly. It is built on four telegraph poles (not full length obviously!) due to an uneven ground and prempting damp problems.
Basically the shed is built without any nails, but instead with timber joints I have made up and dowels through them. But it is also built cheaply, so hence thin wood, and so tricky joints. All the timber frame buildings I have seen on the net have huge pieces of wood; I am afraid my joints will not be strong enough due to their size. But I am not worrying too much about this as I can always stick a few screws in (thank god for metal).
More worringly, I am afraid the wood I am using may be too thin, as I don't really have any experience! The main joists for the floor are 2x4" and there are four of them spanning the length. Will they be strong enough?
The corner uprights are 2x2" but I am thinking of upgrading this: (a) the contents of the shed will be almost entirely on shelves and so rely on these uprights, and (b) I have tried to design the shed using diagonals that translate the forces into the corners. Do you think they should be bigger?
In terms of strength I am most worried about the roof, which will have to take the weight of two humans. It is constructed sparingly with 1x2" wood.
I hope somebody can help me out with this - I'm sure there will be, there's ALWAYS somebody on these forums :You_Rock_. Ooh, and here is a 3D model to help visualize what I mean.
I'll take photos along the build to record and display my bugger-ups, of course.
Basically the shed is built without any nails, but instead with timber joints I have made up and dowels through them. But it is also built cheaply, so hence thin wood, and so tricky joints. All the timber frame buildings I have seen on the net have huge pieces of wood; I am afraid my joints will not be strong enough due to their size. But I am not worrying too much about this as I can always stick a few screws in (thank god for metal).
More worringly, I am afraid the wood I am using may be too thin, as I don't really have any experience! The main joists for the floor are 2x4" and there are four of them spanning the length. Will they be strong enough?
The corner uprights are 2x2" but I am thinking of upgrading this: (a) the contents of the shed will be almost entirely on shelves and so rely on these uprights, and (b) I have tried to design the shed using diagonals that translate the forces into the corners. Do you think they should be bigger?
In terms of strength I am most worried about the roof, which will have to take the weight of two humans. It is constructed sparingly with 1x2" wood.
I hope somebody can help me out with this - I'm sure there will be, there's ALWAYS somebody on these forums :You_Rock_. Ooh, and here is a 3D model to help visualize what I mean.
I'll take photos along the build to record and display my bugger-ups, of course.
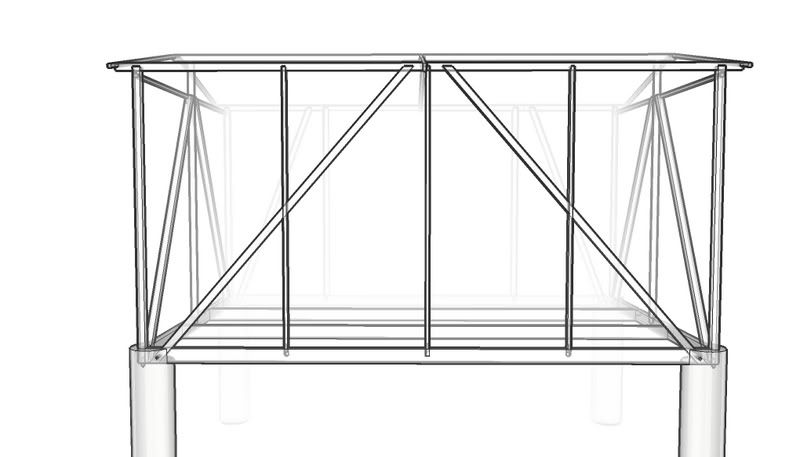
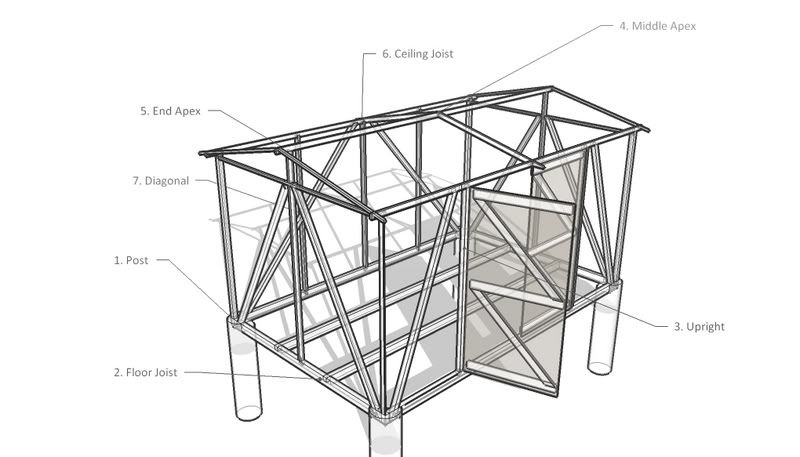
